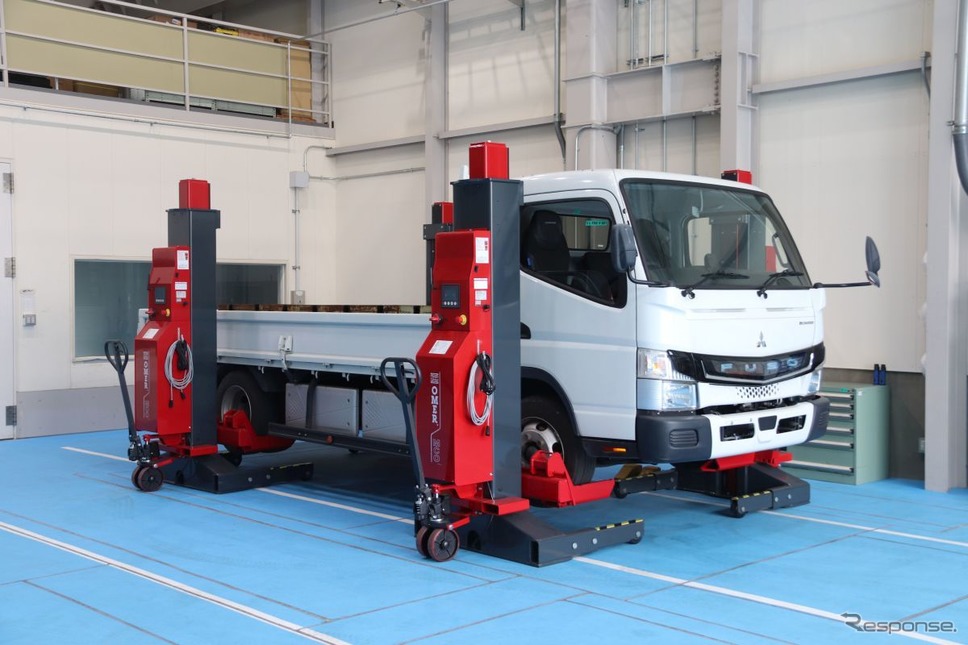
三菱ふそうトラック・バスの喜連川研究所(栃木県)は、報道陣向けに次世代型『eキャンター』の試作モデルを公開した。研究所内に整備・改修したというEVトラック関連のテストベンチなどもあわせて公開された。
EVの開発には、当然バッテリーやモーターをテストする環境が必要だ。エンジン車でもそうだが、特殊な測定やテストは専門の業者や検査機関、あるいは業界団体が運営するテストベッドや試験センターを利用する。だが、認証などが必要な場合以外、独自技術の開発には自前の開発環境、設備は欠かせない。
喜連川研究所では、「eキャンター」の前身である「キャンターE-CELL」を開発した10年以上前からEVの研究開発を行なっている。いくつかの設備は当時のものを工夫して運用しているが、新しい設備投資も行なっている。案内された「エンジン研究棟」では、3つの試験室をEV関連のテストベンチに改装されている。
コンポーネントテストベンチでは、モーターとインバーターが一体化されたeアクスルの試験を行う。もとはディーゼルエンジンのテストベンチだったものをeアクスル用に改造した。設備の大きな変更はバッテリーの代わりをする巨大な電源ユニットと、DC急速充電器。また、内部では高圧を扱うためドアロックは資格保持者のみ入れるようにIDカードのセキュリティシステムが強化された。
テストベンチに取り付けられたeアクスルには、電源装置からの給電ラインと車両ECU他に相当するコンピュータシステムが繋がっている。モーターの出力軸はシャーシダイナモにつながっている。車両の走行パターンや運転操作は、コンピューターに内蔵された数値モデルが制御する。このモデルは道路モデル、車両モデルも用意されており、ダイナモを制御することで、実際の走行条件と同じ負荷を与える。
システムテストベンチは、主にECUの結合テスト、システムテストを行う場所だ。テスト対象は主にモーター・インバーターを制御するECU。テストベンチには実車が据え付けられ、パワートレインECU以外のECUや操作系のエミュレーション(模倣)は実車の各部が行う。実車との大きな違いは、バッテリーモジュールが厳重な保護ケースに入れられていることだ。
テスト中にトラブルや問題があり、バッテリーが加熱したり発火しても大丈夫なように鉄製の密閉容器に覆われている。緊急時は内部に大量の水を流し込みバッテリーを冷却できるようになっている。バッテリー火災は、化学反応なのでとにかく温度を下げることが一番と言われている。泡や薬剤で炎を消しても消火にならない。
これと同様なものはバッテリー分解室にも見ることができる。ここは、走行試験などを行なったあとのバッテリーの状態を分解して確認する。分解といっても、モジュールを開けてセルごとに分ける作業だ。セル内部のラミネートパックや電池そのものを分解するわけではない。電極や電解質など内部の状態を確認する場合は、専門の検査機関や事業者に依頼するそうだ。
分解されたセルの状態や電圧、温度など試験項目によって必要な測定器を持ち込みさまざまな検査を行うという。ここでも発火や破裂事故への対応を考える必要がある。分解台はじつは巨大な水槽になっており、本体横の緊急ボタンを押すと、台が下降して下の水槽にバッテリーごと水没させる。また、爆発などに対処するため、天板はファネル状になっており、これも緊急ボタンで上下する。天板が降りてきて水槽全体を密閉しつつファネル部が圧力を外に逃すしくみだ。
この装置は最近できたもので、これまでの開発作業のニーズで生まれたもので喜連川工場独自のものだそうだ。
研究所にはABB製の175kWのDC急速充電器2機も増設された。充電ケーブルはCHAdeMO(3.0またはChaoJiではない)とCCS2に対応している。CCS2は欧州で一般的な充電規格だ。2台あるのでCCS2の350kW充電にも対応させることができるそうだ。CHAdeMOは現行規格対応なので90kWまででの充電となる。CHAdeMOの規格としては150kWも対応しているが、この出力だとケーブルを液冷にする必要があり、国内での実装例はまだない。
喜連川研究所がCCS2の充電器を用意するのは、EVトラックのグローバル展開を考えていることと、三菱ふそうがダイムラーグループであり、研究設備の共有や社内規格や開発基準もグローバルに合わせる必要があるからだ。
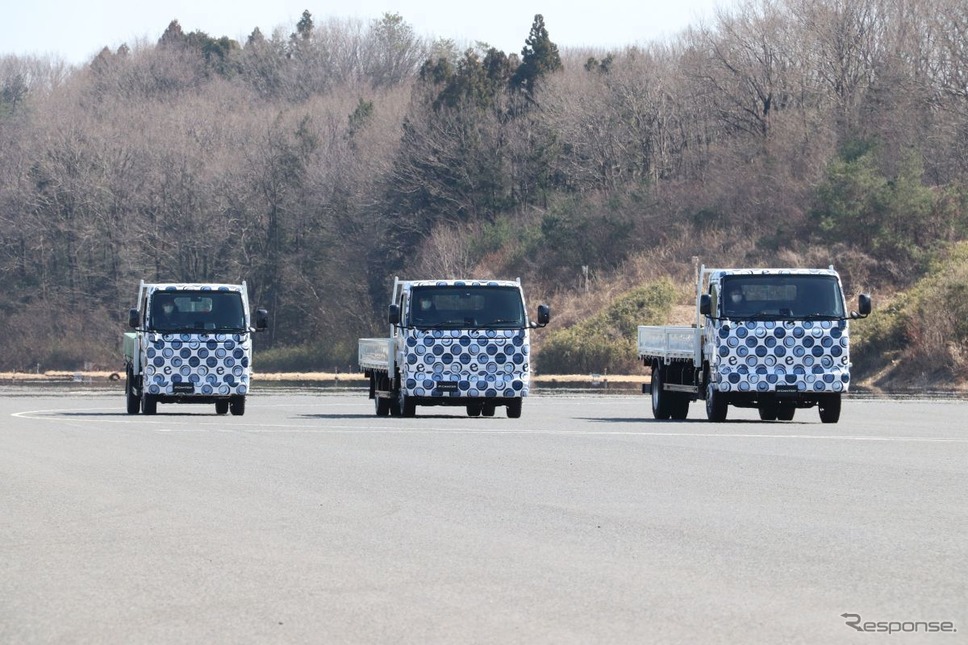
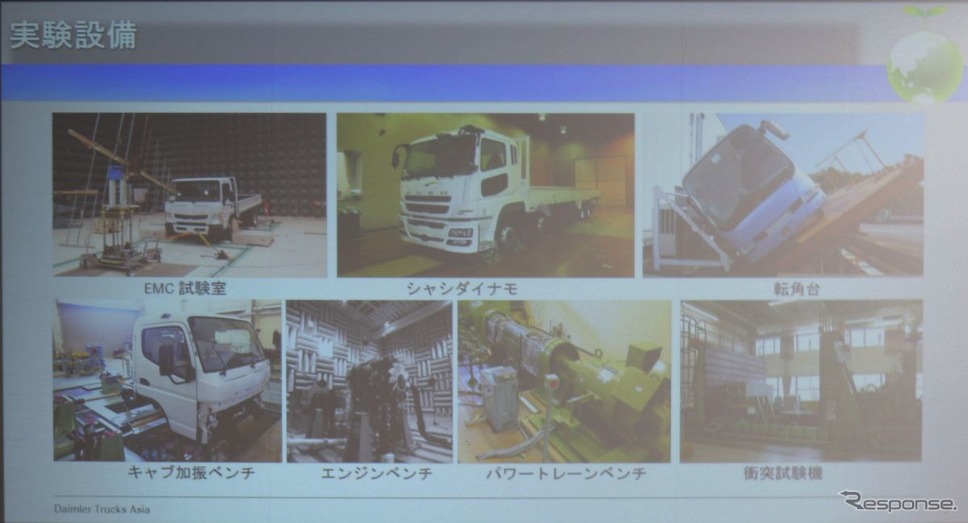
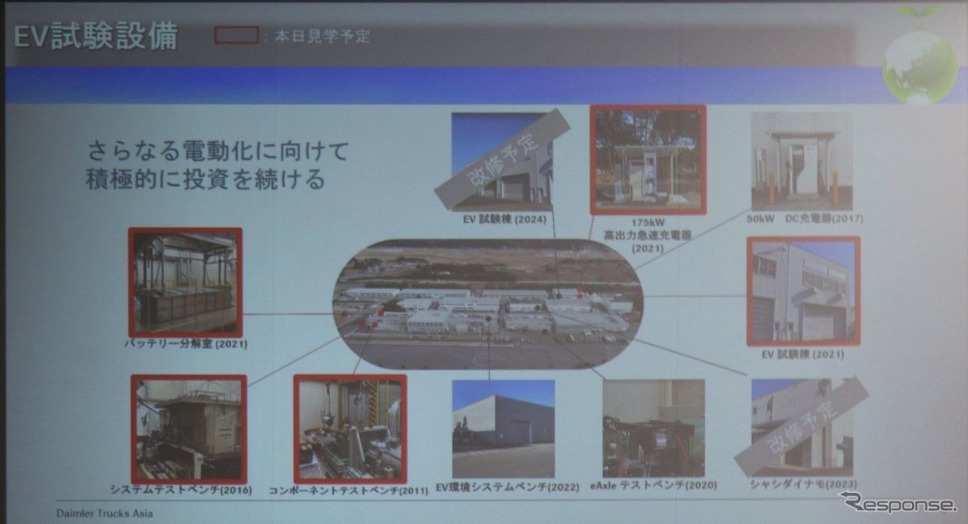
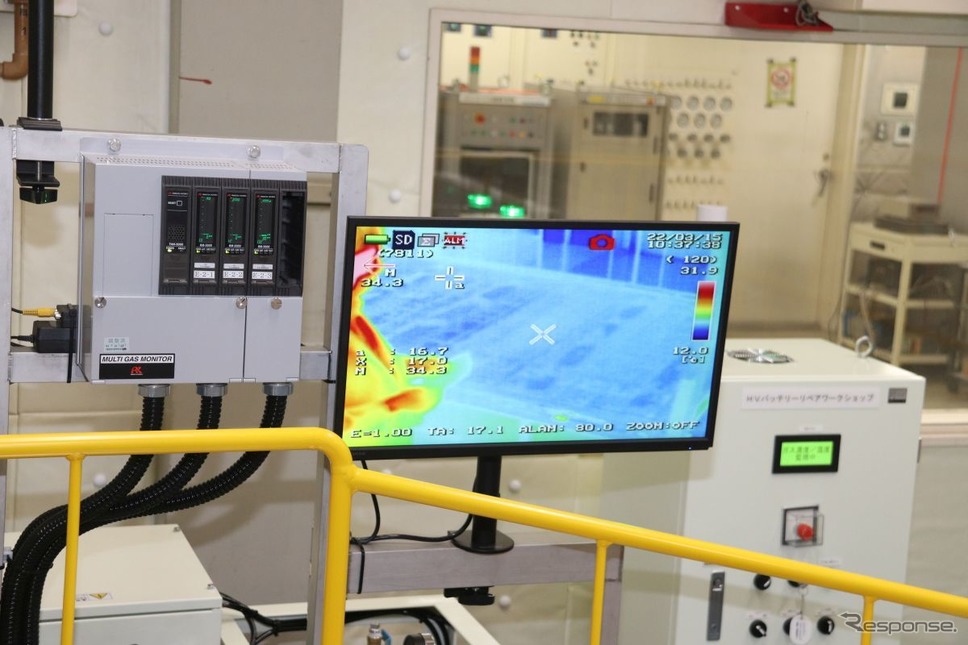
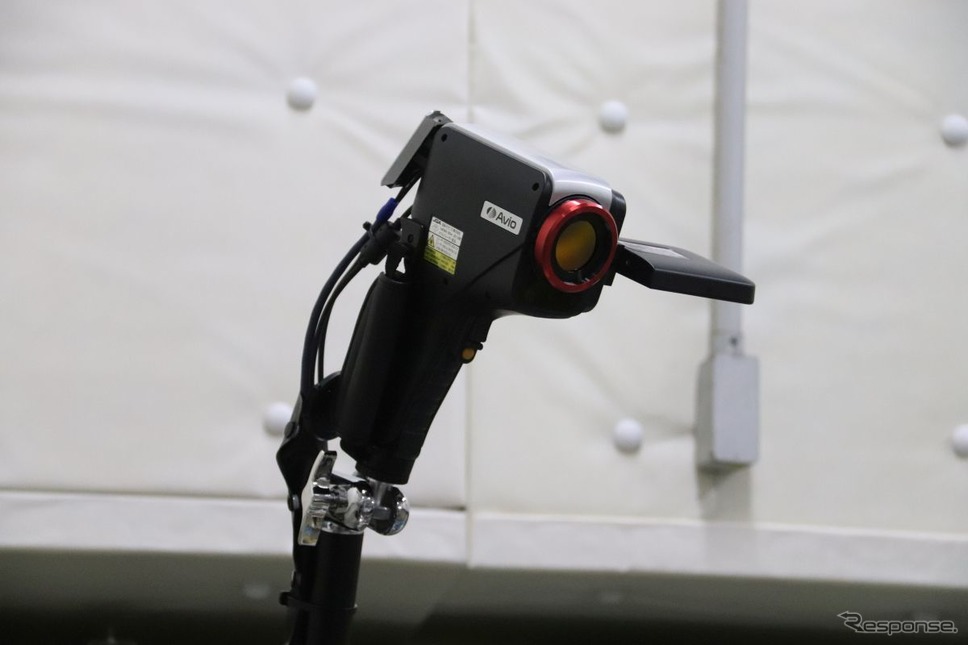
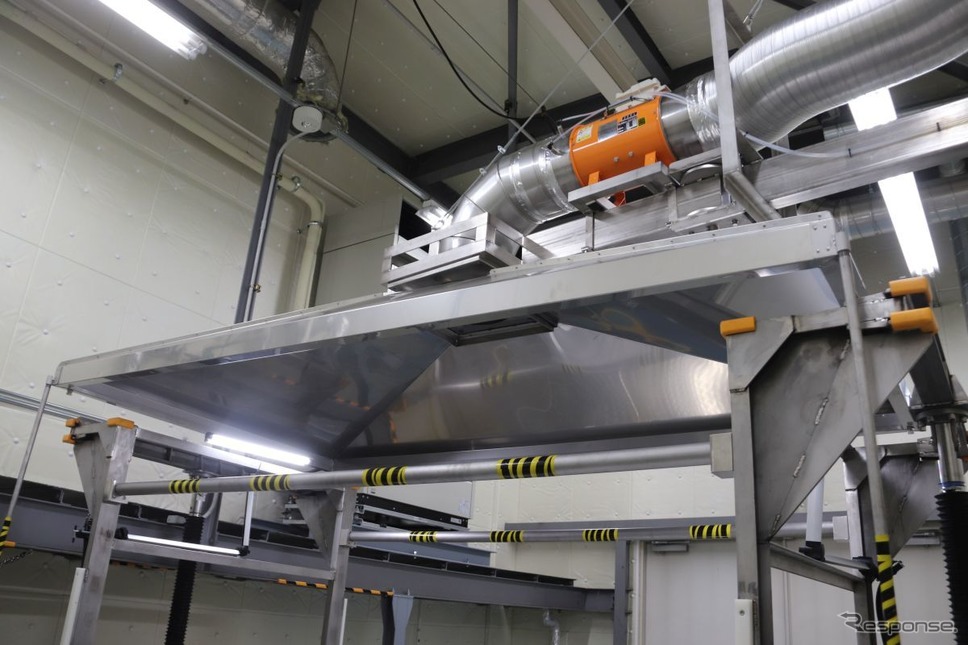
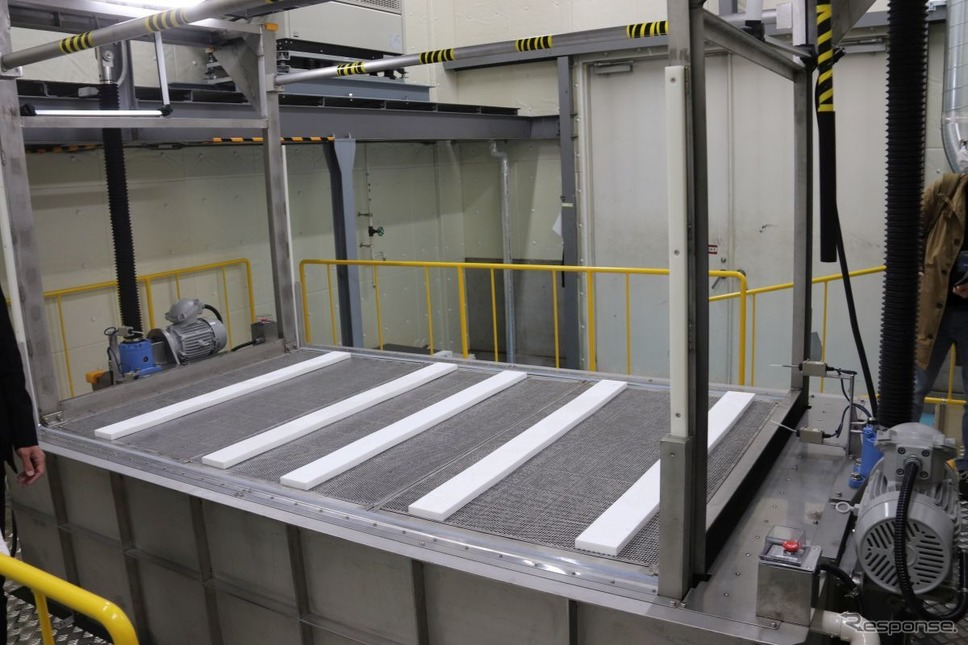
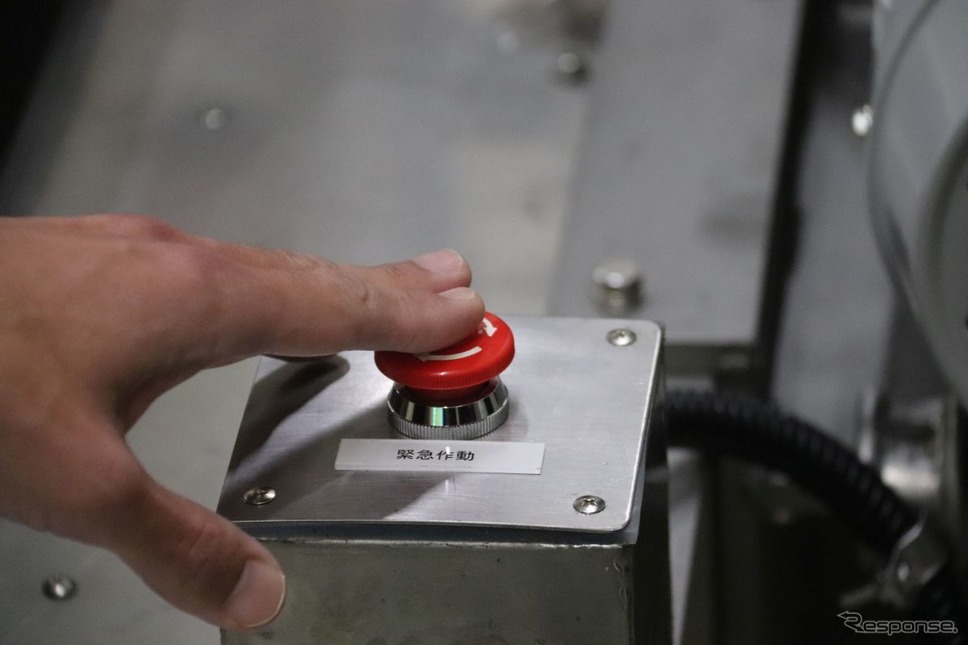
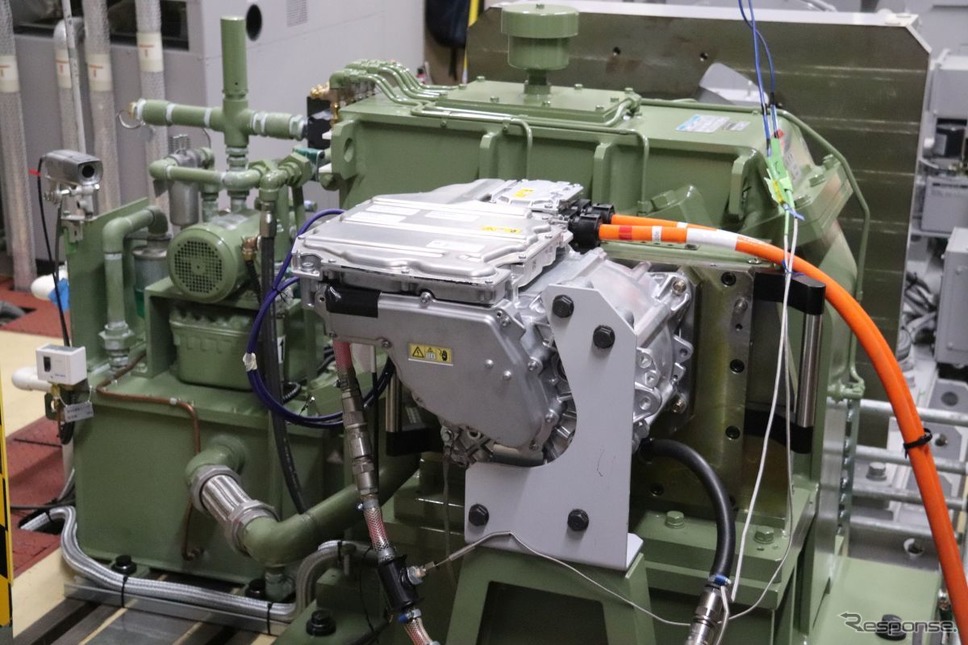
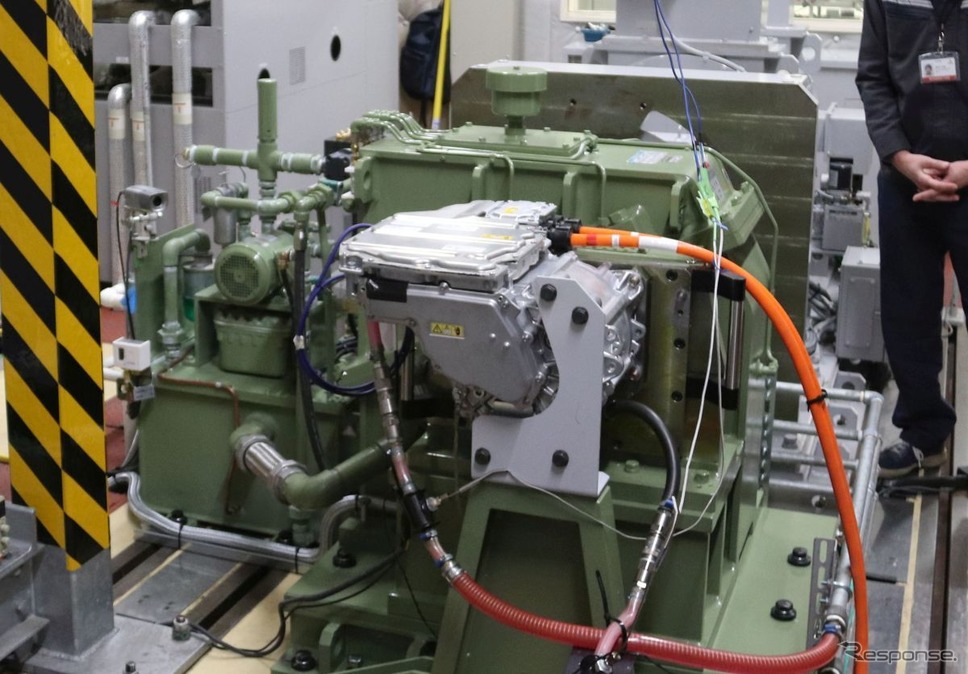
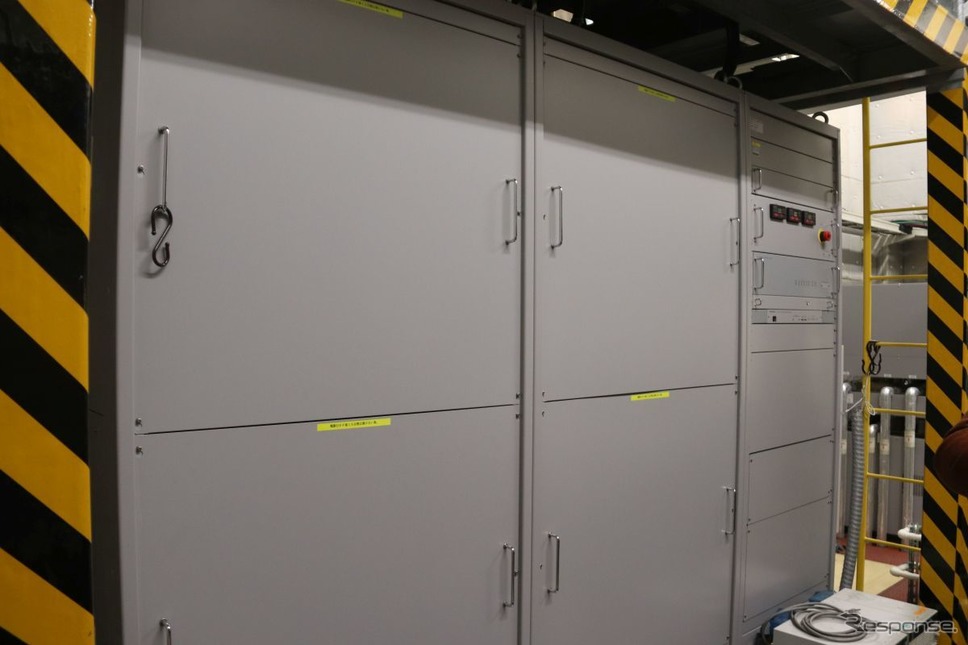
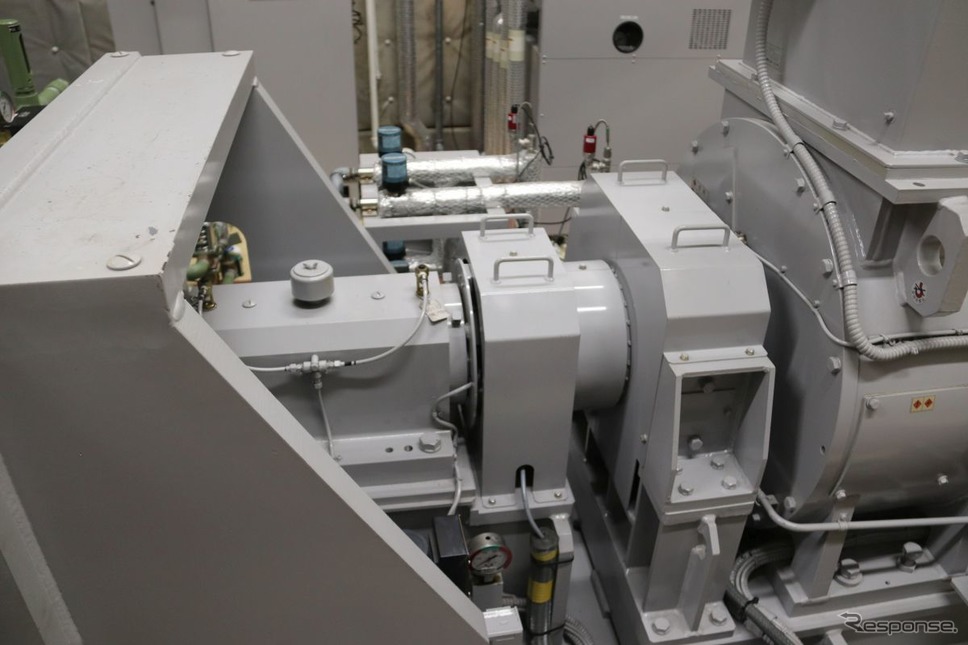
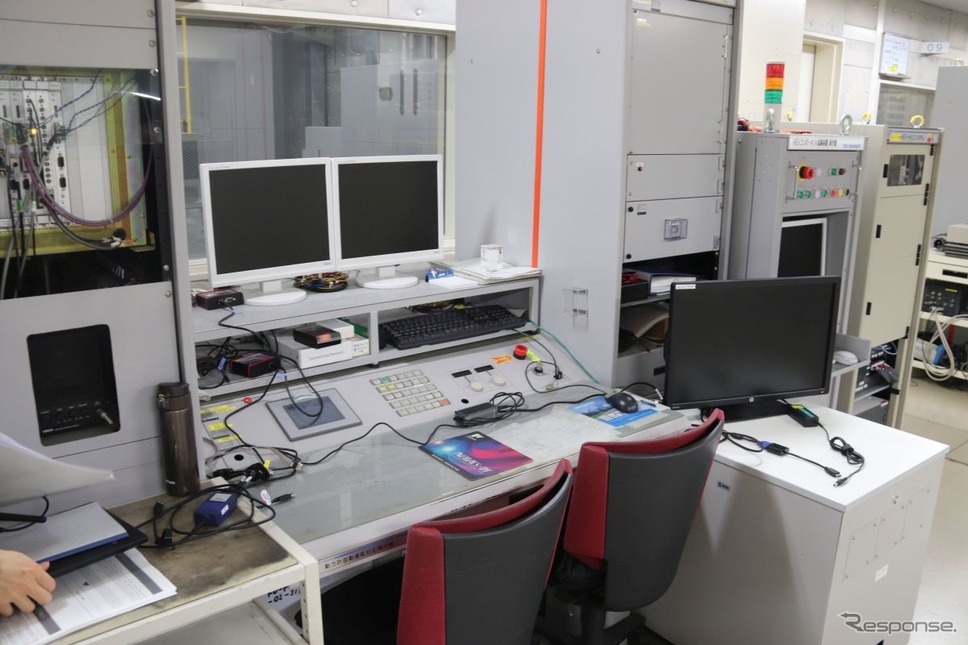
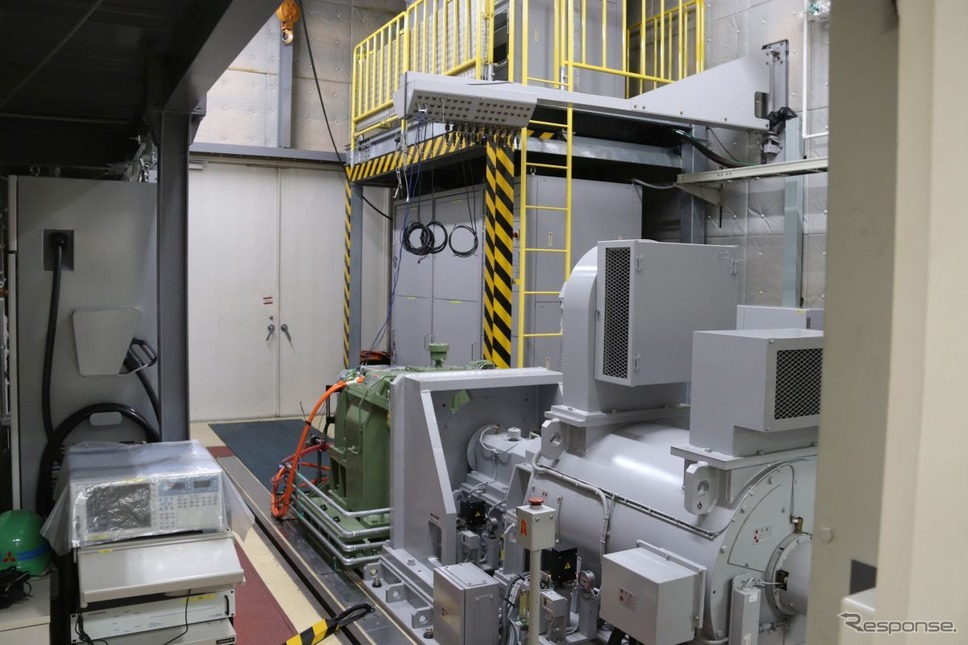
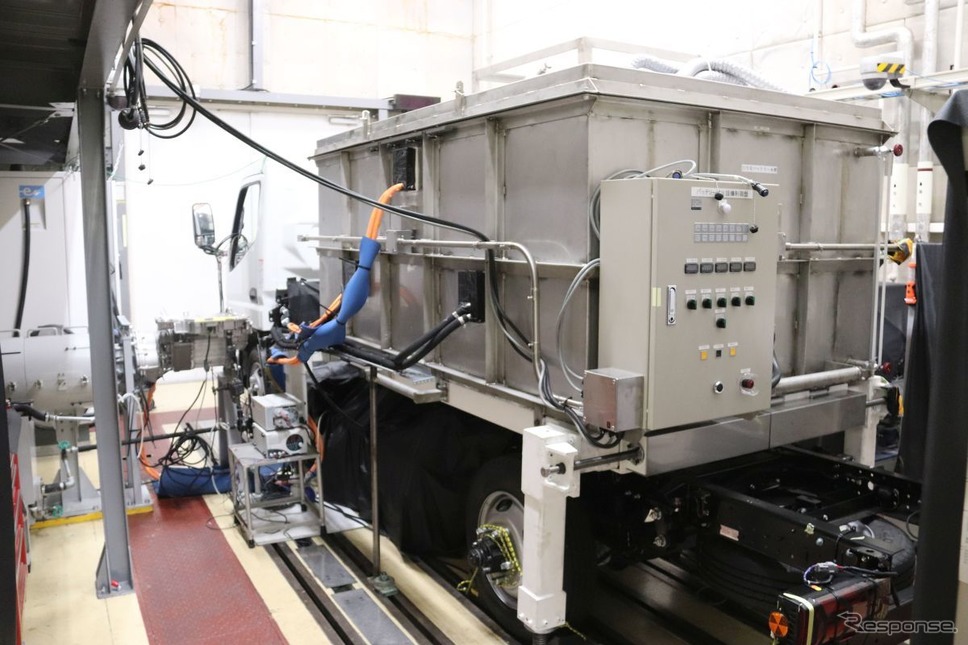
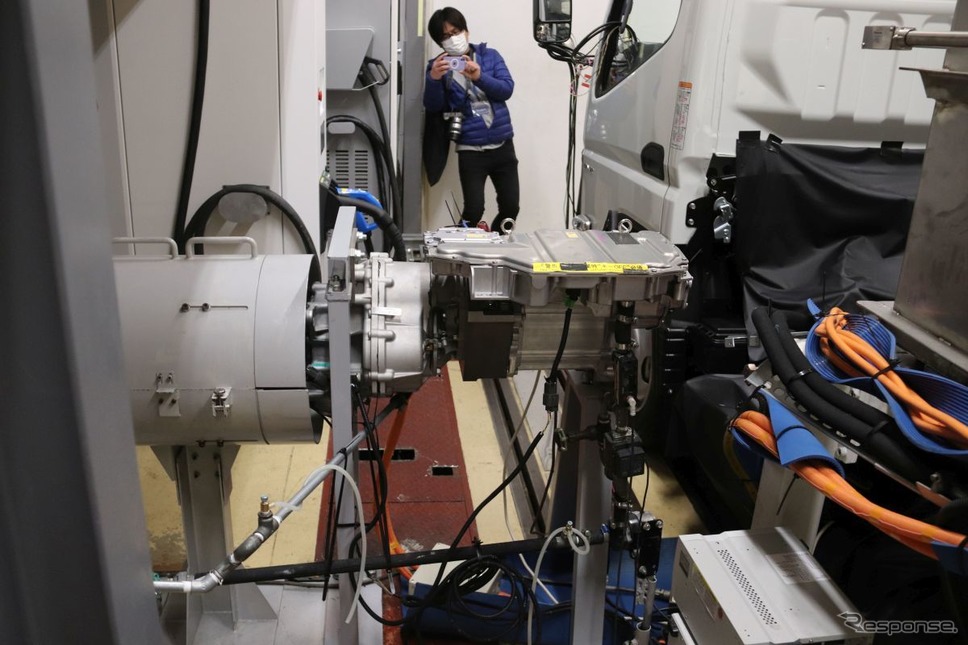
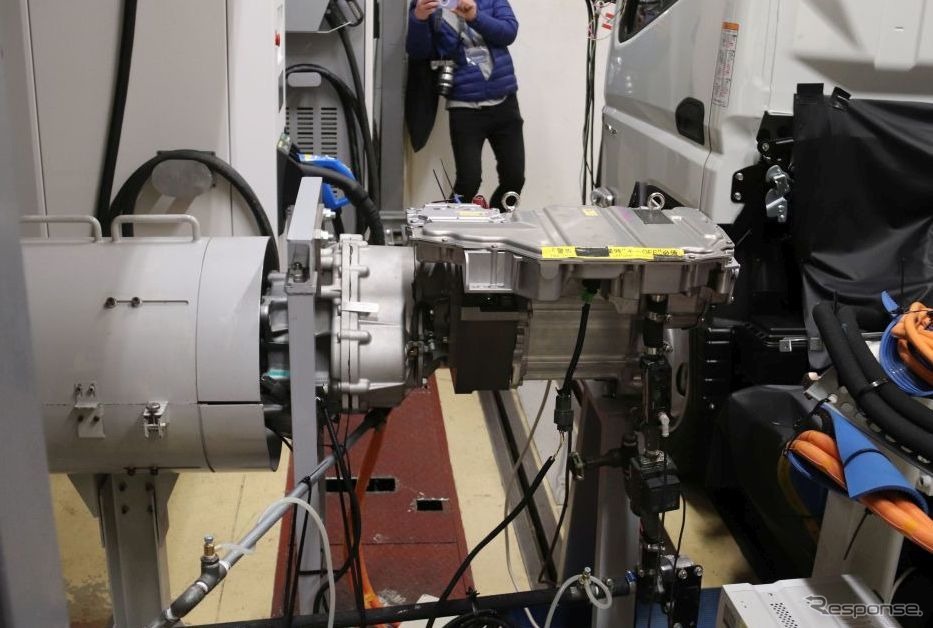
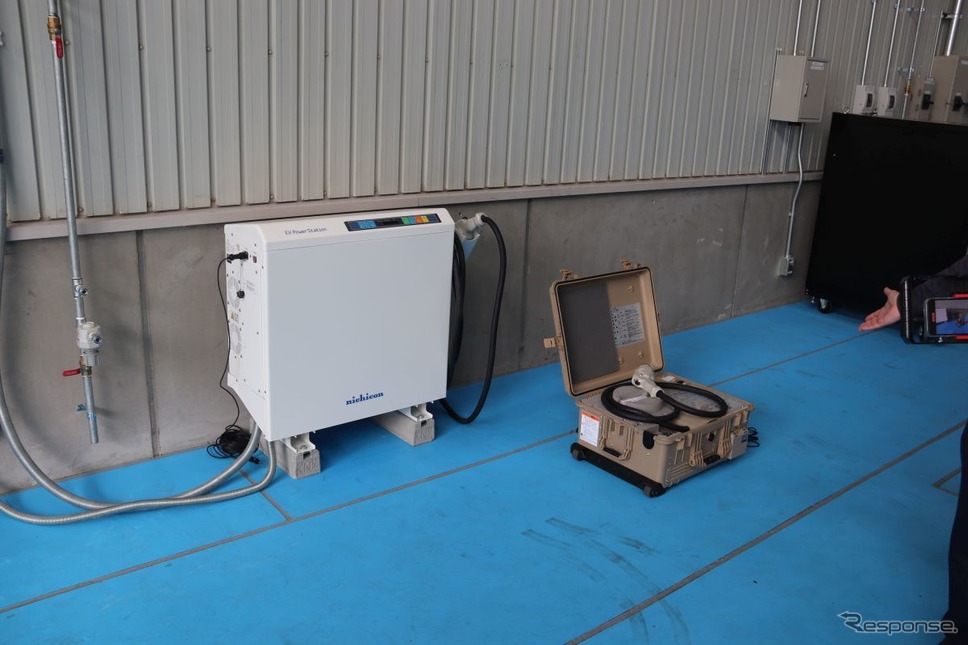
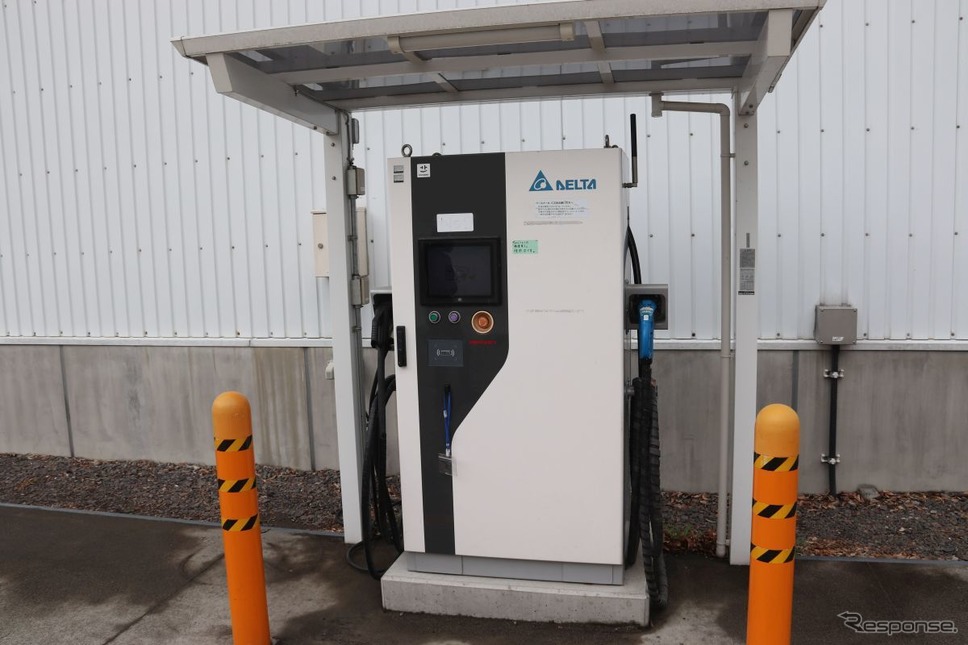
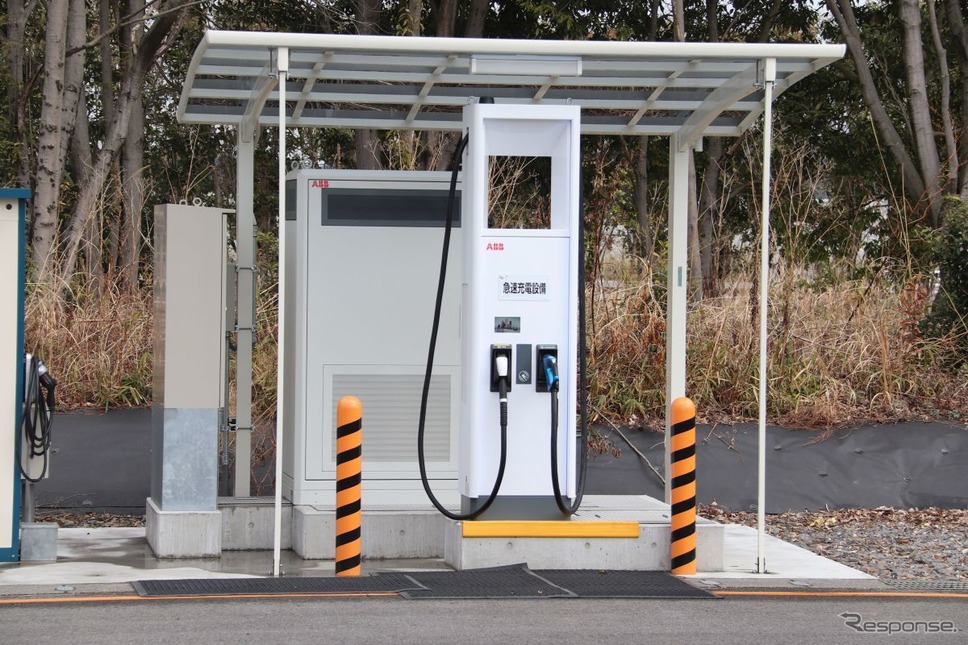
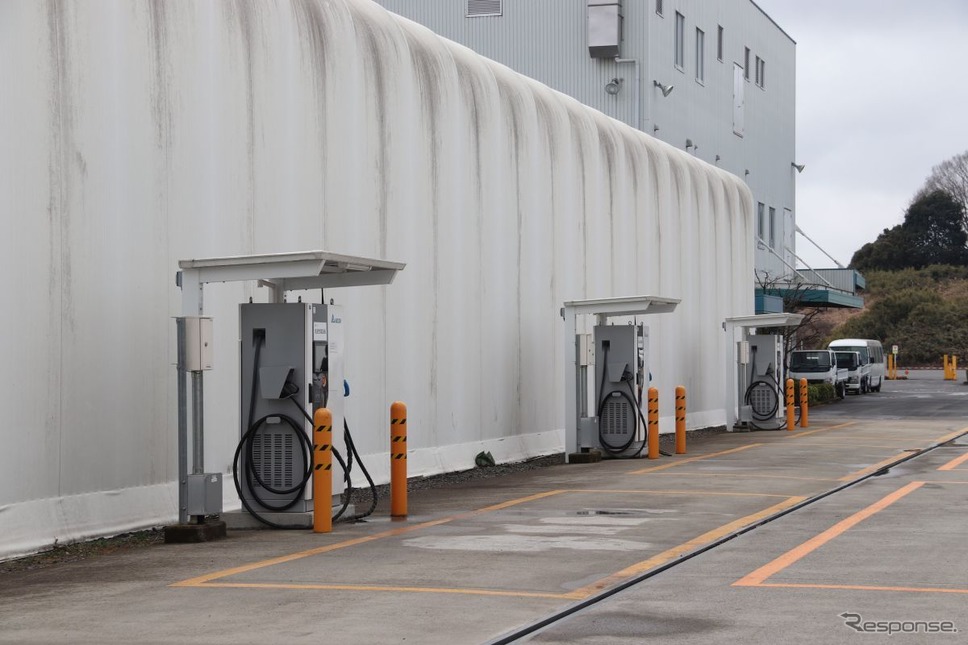
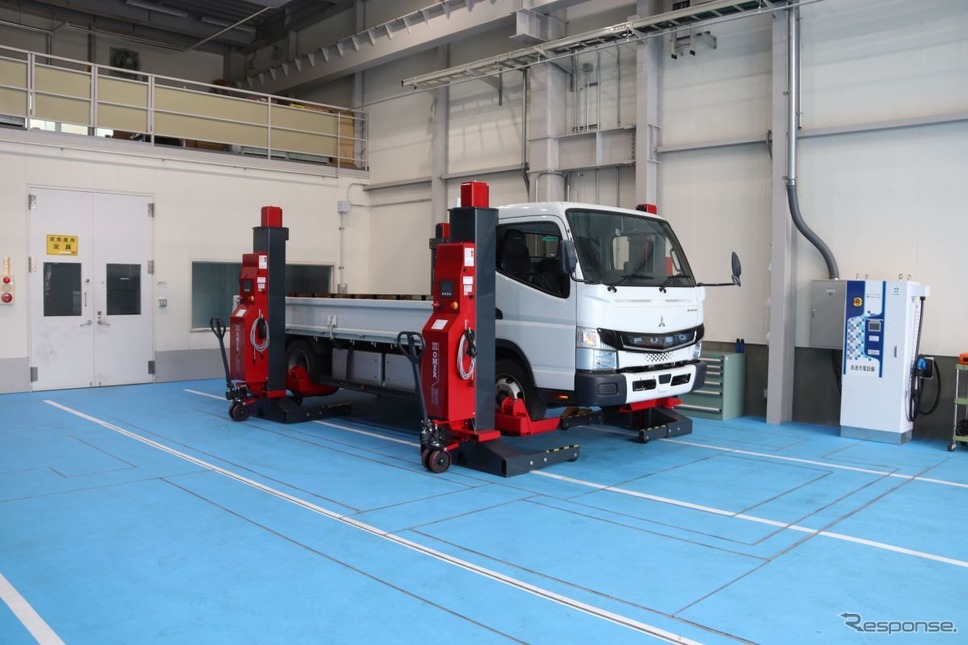
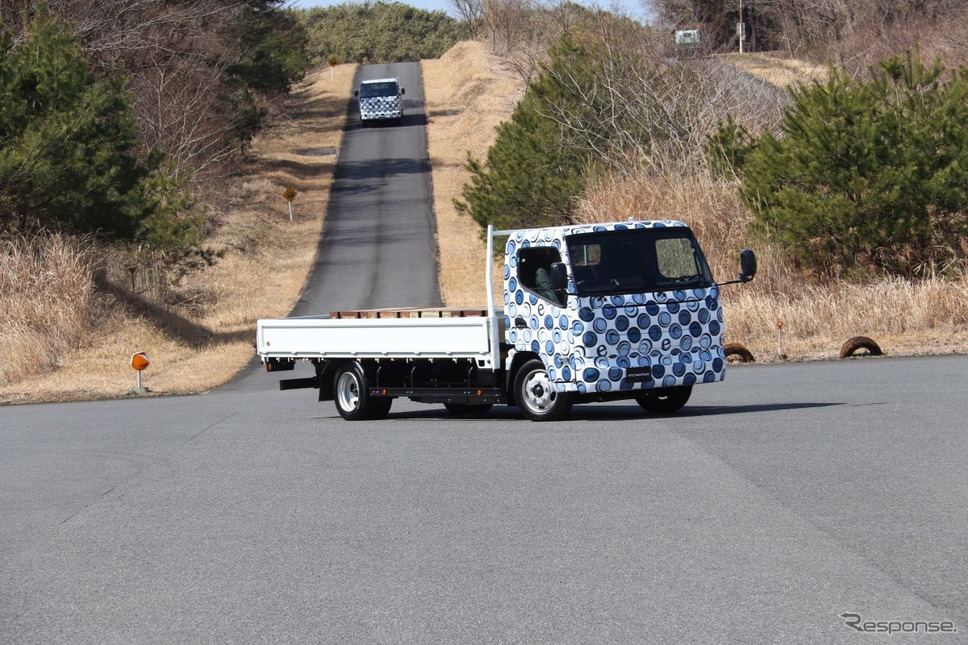
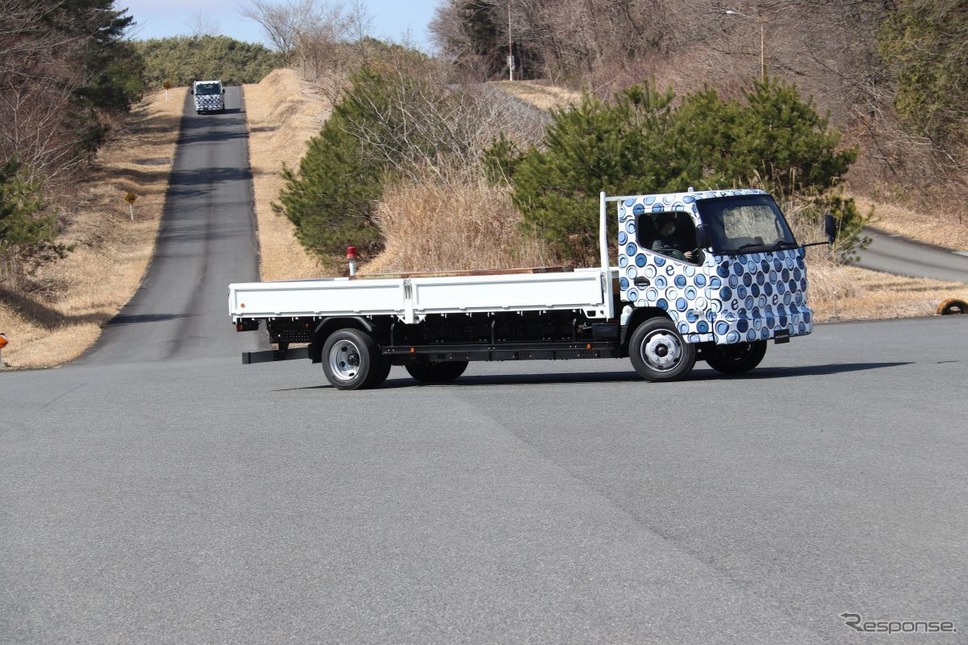
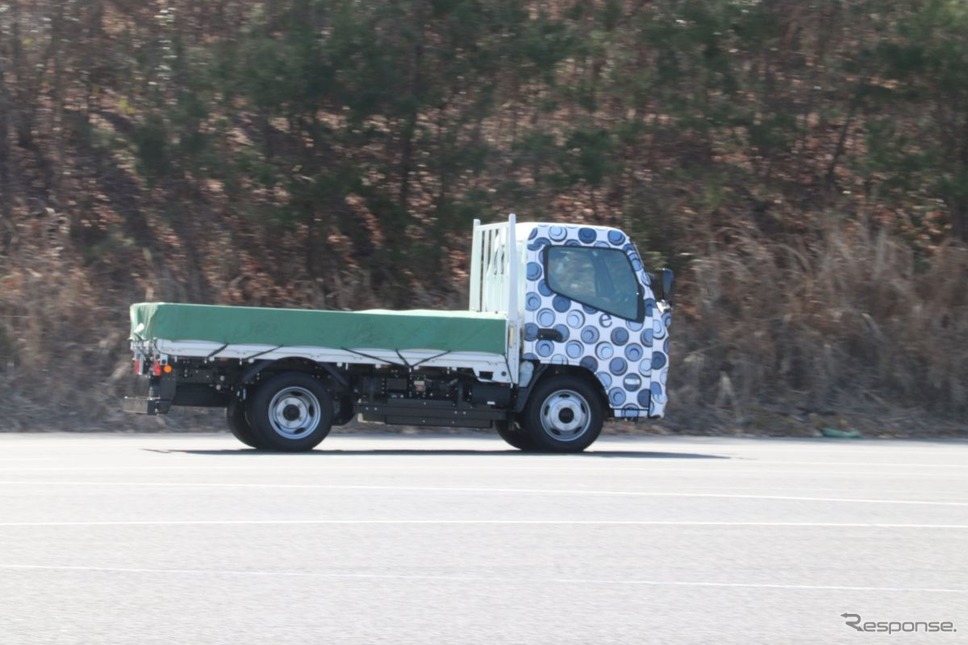
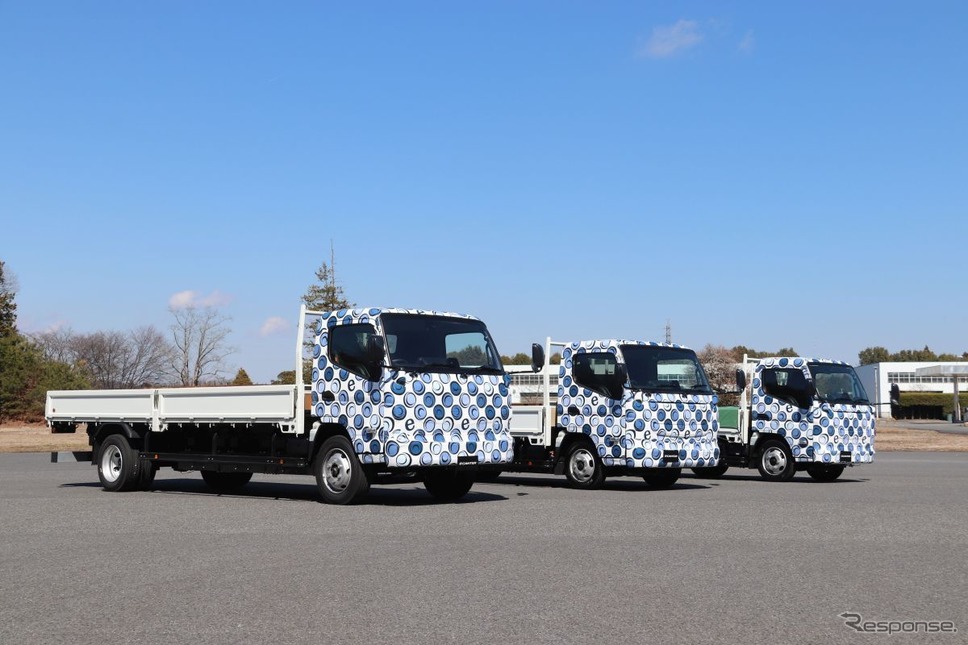