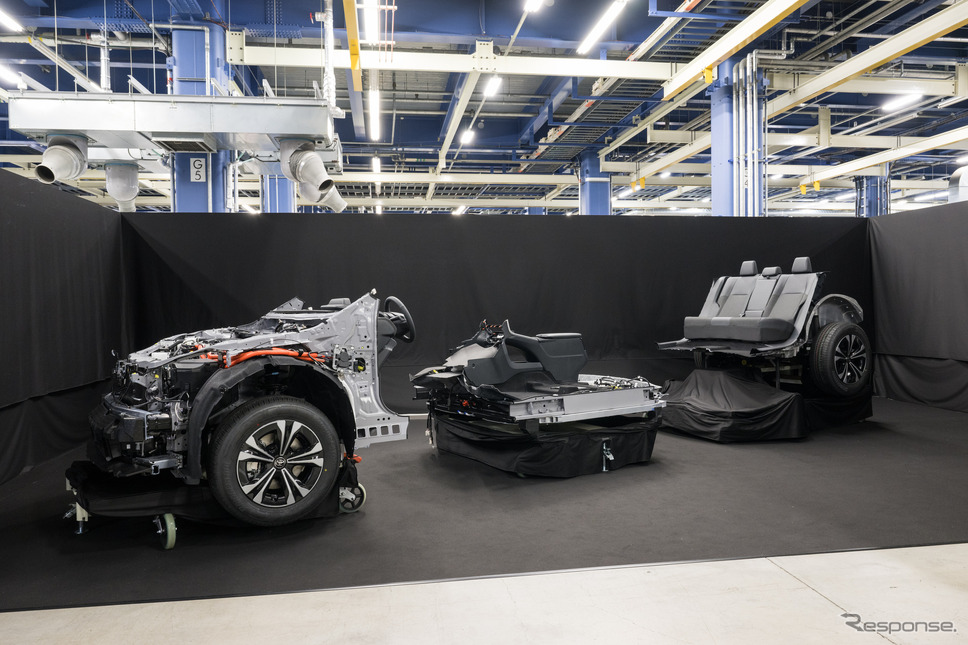
トヨタ自動車は、一部報道向けに「クルマづくりの未来を変えていこう」をテーマとした説明会「トヨタモノづくりワークショップ」を開催。6月に発表したBEV向け全固体電池や、生産工程を大幅に削減する生産技術のギガキャスト、コンベアをなくした自走による生産ラインをはじめ、モノづくりにおけるトヨタらしさの継承と進化を、貞宝工場、明知工場、元町工場という3つの工場の特徴と、それぞれの異なる取り組みとともに紹介した。
新郷和晃CPOは、トヨタの強みをTPS(トヨタ生産方式)を基軸とした「リードタイム短縮」と、時代の変化への対応力だとして、「トヨタの持つ技とデジタル・革新技術で、工程2分の1を実現する。また開発と生産の垣根をなくし、新しいモビリティをすばやく提供する。そして工場カーボンニュートラルや物流などモノづくりの基盤の課題解決にも取り組んでいく」と決意を表明。変革の時代に合わせてモノづくりの未来を変えていくとした。
◆デジタルツインと「匠」の技術の融合
トヨタのモノづくりの原点は、トヨタグループ創始者である豊田佐吉にまでさかのぼる。「毎晩夜なべをして機織り仕事をする母を助けたい」との想いから人力織機を開発した、その精神が自働化とジャストインタイムによるTPSに基づく「人中心」のモノづくりの現場に受け継がれているという。その代表例として今回公開されたのが、貞宝、明知、元町の3工場だ。
まず貞宝工場は、2021年に「スタートアップスタジオ」を開設。以来、高まる新たなモノづくりニーズに素早く対応するためアイデアをスピーディに具現化し、試作開発、量産技術開発に取り組める環境を整備。設備づくりにデジタルツインを取り入れ、3Dモデルを活用することで完成度の高い生産設備の導入を実現する。これにより、生産性を3倍、従来比での改善リードタイムを3分の1にしたという。
同時に、匠(たくみ)と呼ばれる職人の技術の伝承を、デジタル技術によって見える化、解析することで次世代の人材育成にも活用する。
さらに貞宝工場では、2027〜28年の実用化をめざすBEV用全固体電池の開発ライン、2026〜27年の実用化をめざす次世代普及版バイポーラ型リチウムイオン電池の開発ラインを備え、それぞれ製品開発や量産工法の開発に取り組んでいる。今回はバイポーラ型リチウムイオン電池の工法の一部として、塗工行程が公開された。ハイブリッド車で培った電池生産技術と、燃料電池車で開発した高速塗工技術を応用した設備で、量産を見据えたスピードでリン酸鉄リチウムのペーストを大量に金属箔に塗ることができる。
◆86もの部品を1つにする、ギガキャスト技術
明知工場では、匠の技を最大限に発揮するモータースポーツ用エンジン部品の生産工程を見せた。レースで使われる高性能エンジンは量産エンジンと比べても内部構造が複雑で、かつ日々性能を向上させるためスピードが求められる。匠による木型、砂型で作られた中子(なかご)を用いたアルミ鋳造技術によりこれを実現。匠の技とレースの現場で鍛えられた知見は、量産車に搭載されている高効率なTNGAエンジンに生かされている。スーパー耐久をはじめ、トヨタがアピールする「モータースポーツを起点としたもっといいクルマづくり」の原点ともいえるのが、この匠の技術だと言える。
また同じ鋳造技術でも、特に次世代のクルマづくりに向けてトヨタが注力するのが「ギガキャスト技術」だ。この試作機が、明知工場で稼働している。ギガキャストは、車体の3分の1にあたる部分を一気に成形する鋳造技術で、今回公開された車体の後方部分では86もの部品を1つの部品として成形することで大幅な工程短縮を実現する。このギガキャストでは定期的な鋳造の型の交換が必要で通常はその交換に24時間程度を要するが、このリードタイムを約20分まで短縮する金型を開発。稼働停止にともなうムダを削減する。現在は独自の解析技術を用いながら鋳造の品質向上、不良品の発生を抑えるための開発をおこなう。
◆混流、自動搬送による次世代の生産ライン
最後の元町工場は、トヨタが押し進める「マルチパスウェイ」を支える様々なパワートレーン(BEV、FCEV、HEV、ICE)や、異なるボディタイプ(セダン、ミニバン、SUV)のクルマを同一のラインで生産するための技術や現場づくり、クルマの個性を高める匠による加飾技術を見せた。
混流生産ラインでは『クラウン』『bZ4X』『ミライ』『ノア』『ヴォクシー』、そしてパトカーと様々なモデルが生産される。1台あたりの作業時間では最も工数の差があるミライとbZ4Xで2.5時間も異なる。これを平準化してラインに流すことでその差を最大30秒まで縮める。ラインを流れる車体の土台(トレー)を、さまざまなボディタイプやパワートレインに対応できる形に改善、作業者の負担を軽減する“からくり台車”を手作りで開発するなどし対応する。
さらに次世代BEVの生産ラインとして、ギガキャストによりフロント、センター、リアの3分割によるモジュール構造とすることで作業者が乗り込むことなくシートなどの取り付けができる様子、自動運転技術と工場のセンサーによる完成車の自走搬送のデモンストレーションを公開。自動搬送は工場のベルトコンベアを必要とせず、これを次世代BEVラインに適用することで、ラインレイアウトの柔軟性が大幅に向上。生産準備のリードタイムと工場投資を大幅に削減することができる。すでに一部の溶接工程ではコンベアを使わない工程を実装しており、課題の洗い出し、次世代BEVラインの設備開発を進める。
加飾技術では、新型『センチュリー』に採用されたシャープなキャラクターラインを成形するレーザー加工技術、同車のスカッフプレートに精巧な槌目模様を入れる匠の板金技術、今後発表される『クラウンスポーツ』のバンパーに採用する塗装なしで艶のあるピアノブラックカラーを実現する金型技術などを公開。人の手による高い技術力をアピールした。
◆新しい時代を切り拓き、幸せの量産を目指す
また、「物流24年問題」によるドライバー労働時間短縮やドライバー不足への対応にも取り組む。具体的には、完成車の物流の改善だ。全国の工場や港の積込み/荷卸し場に屋根を設置し悪天候でも安全に作業できるようにした。さらに完成車ヤードでの車両運搬にVehicle Logistics Robot(VLR)と呼ばれる車両搬送ロボットを導入し、自動でキャリアカーの積載場までの搬送をおこなうことができるようにする。
管制システムが複数台のロボットの動きを一括管理することで、安全を監視しながら最適経路での搬送をおこなう。人的負担の軽減だけでなく、人による運搬と異なりドアの開け閉めが不要なため、隙間なく効率的に車両を配列するヤードの効率的な活用も可能になる。こうした発想もすべて、トヨタの「人中心」の考え方によるものだ。
新郷CPOは、「トヨタはこれまでもこれからも、人を中心に、誰かの笑顔のために仕事をする現場、『ありがとう』が自然に溢れ、イキイキと働ける工場をつくることで、新しい時代を切り拓き、幸せの量産を目指していく。トヨタの技で、クルマの未来を変えていこう!」と声を上げた。
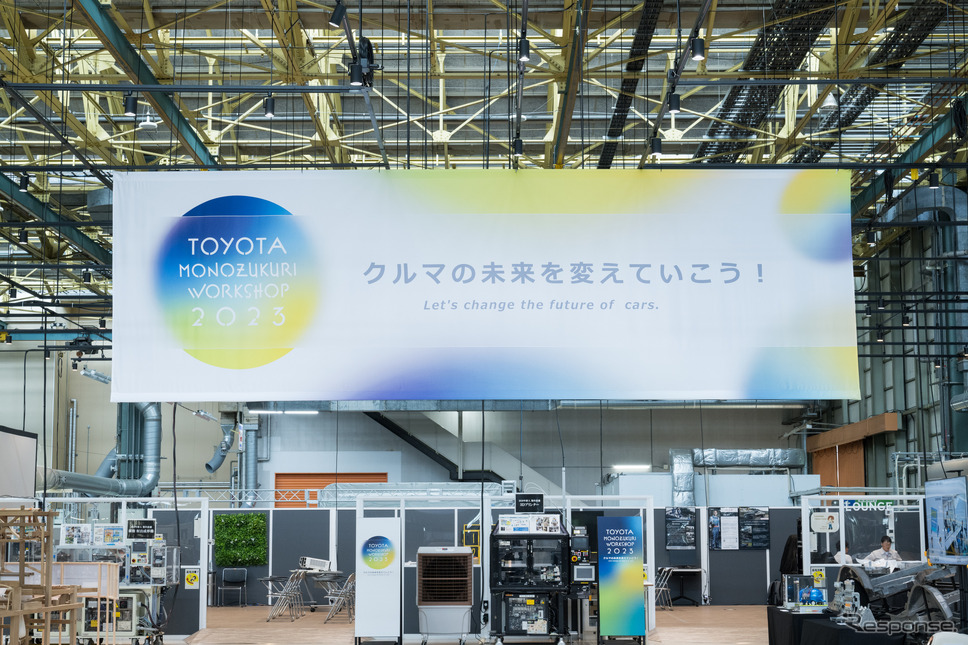
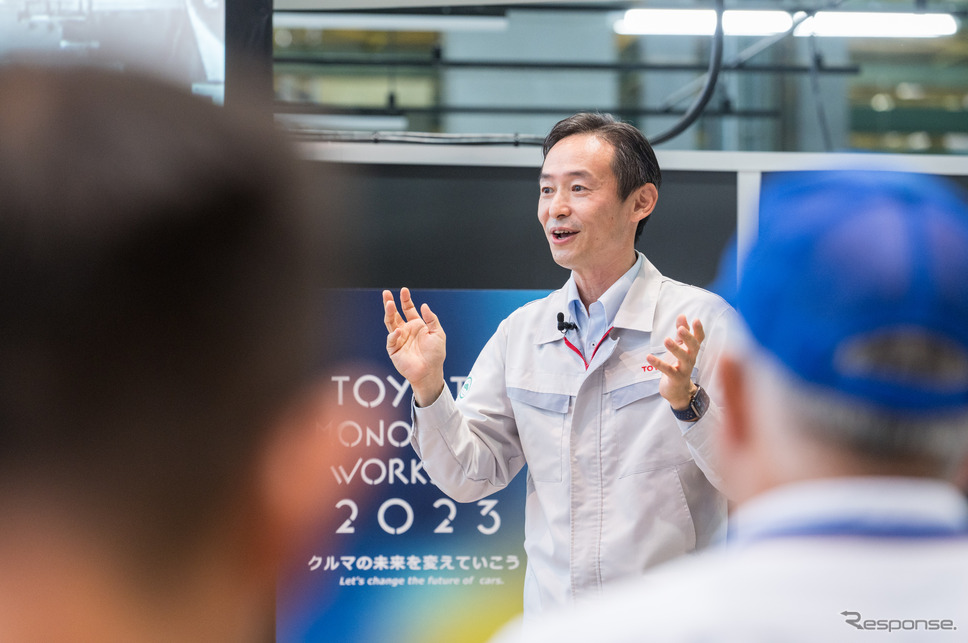
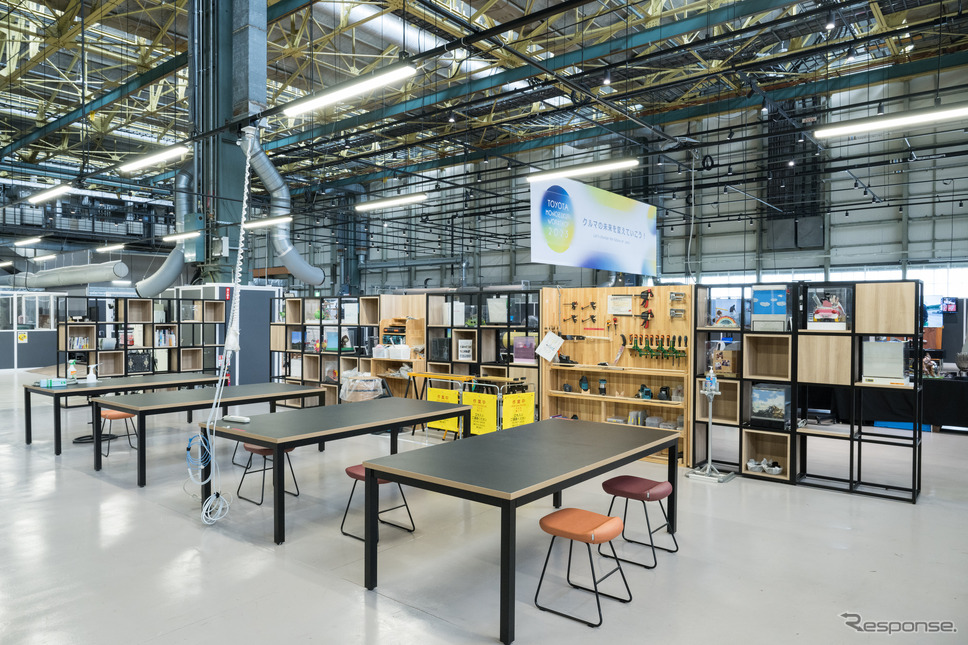
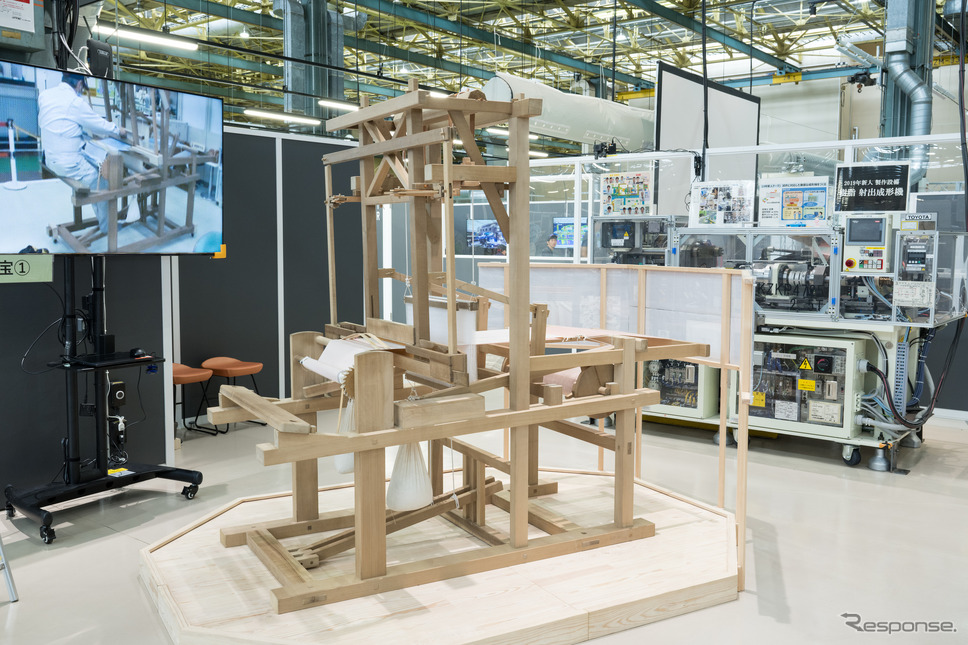
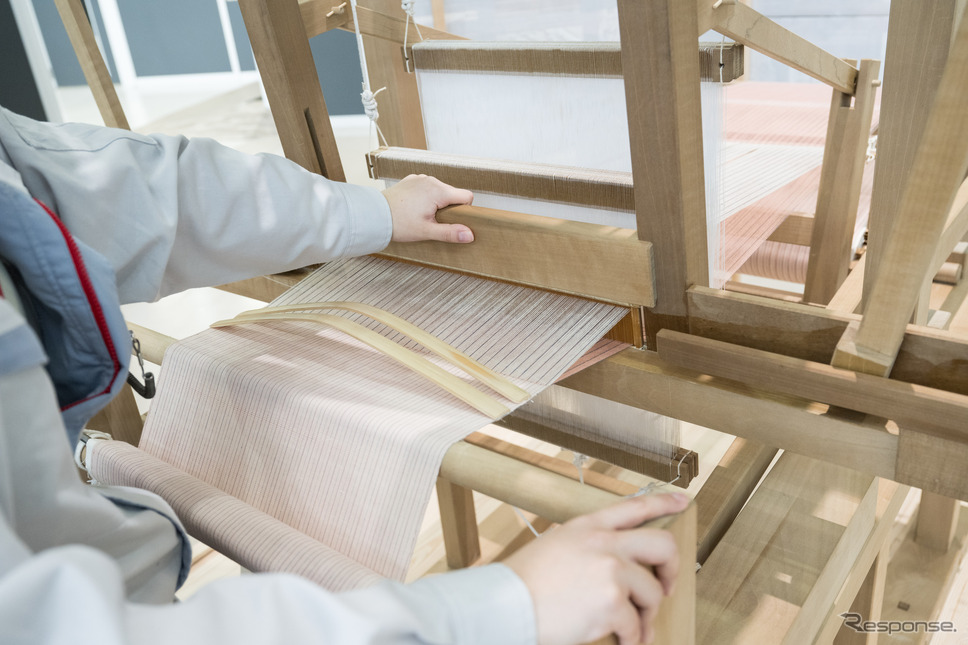
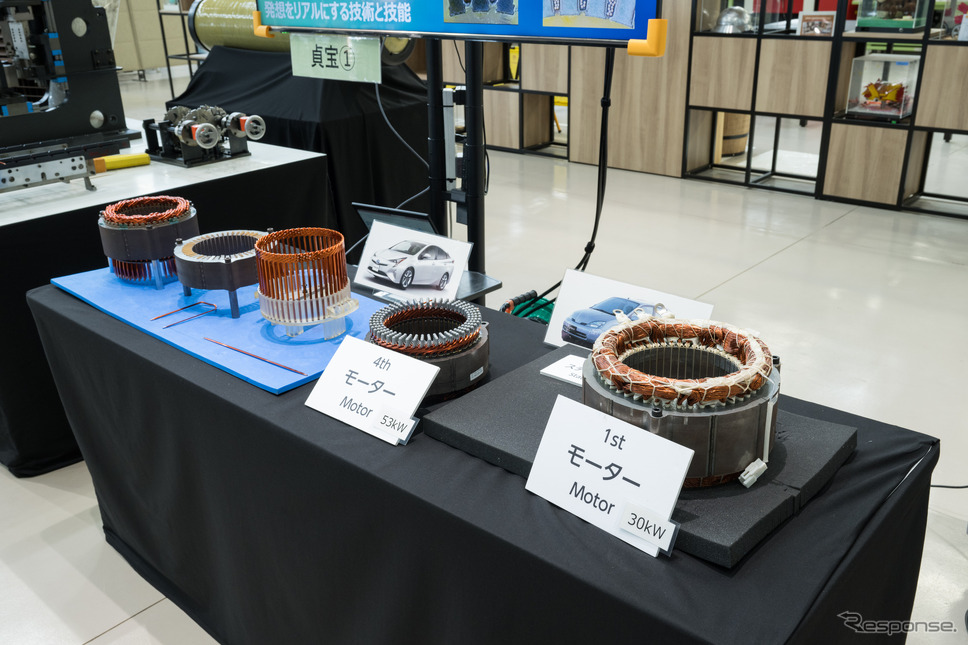
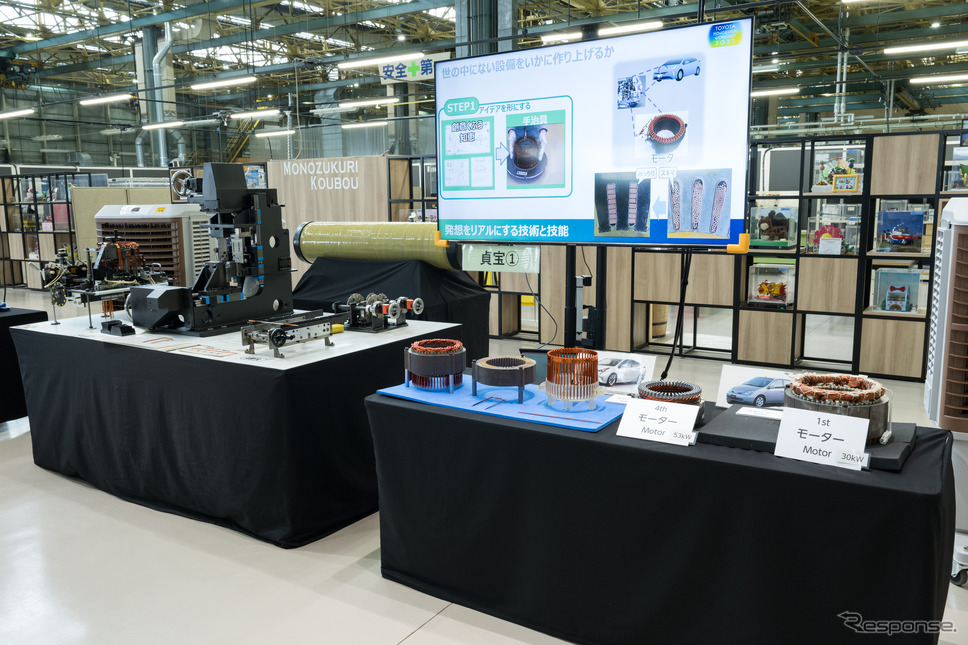
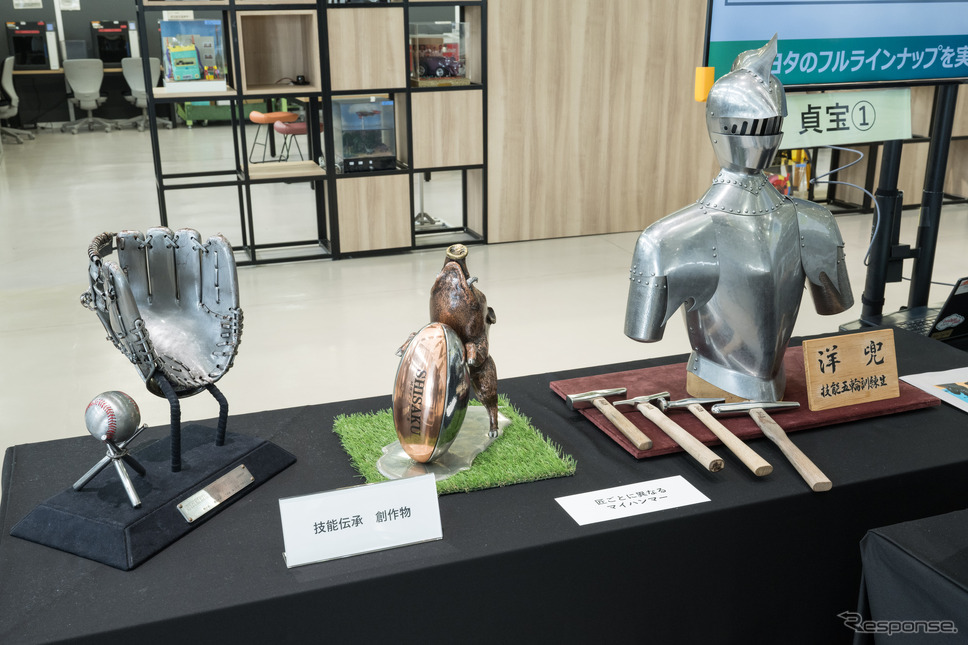
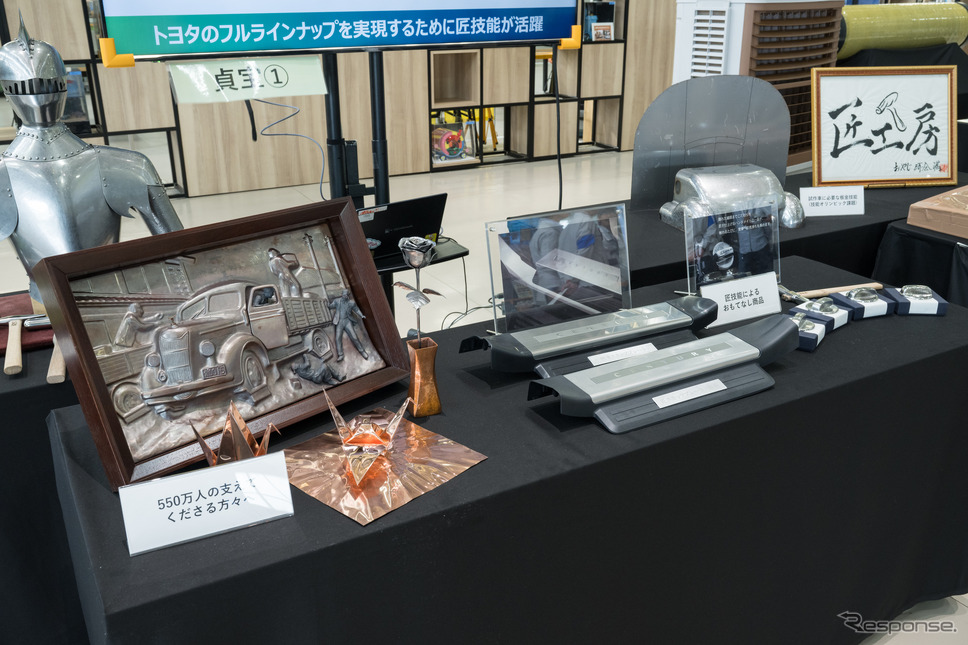
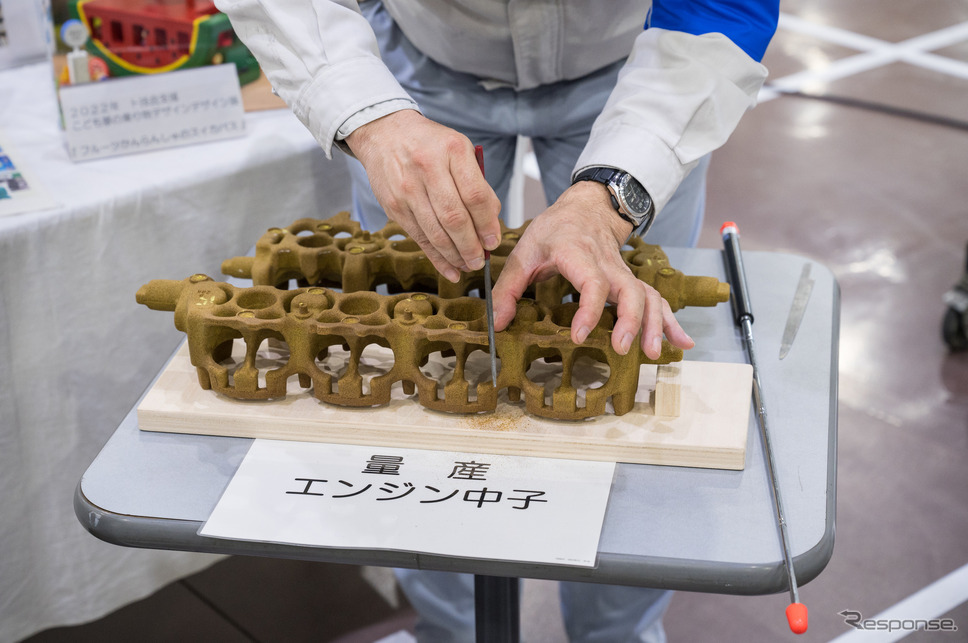
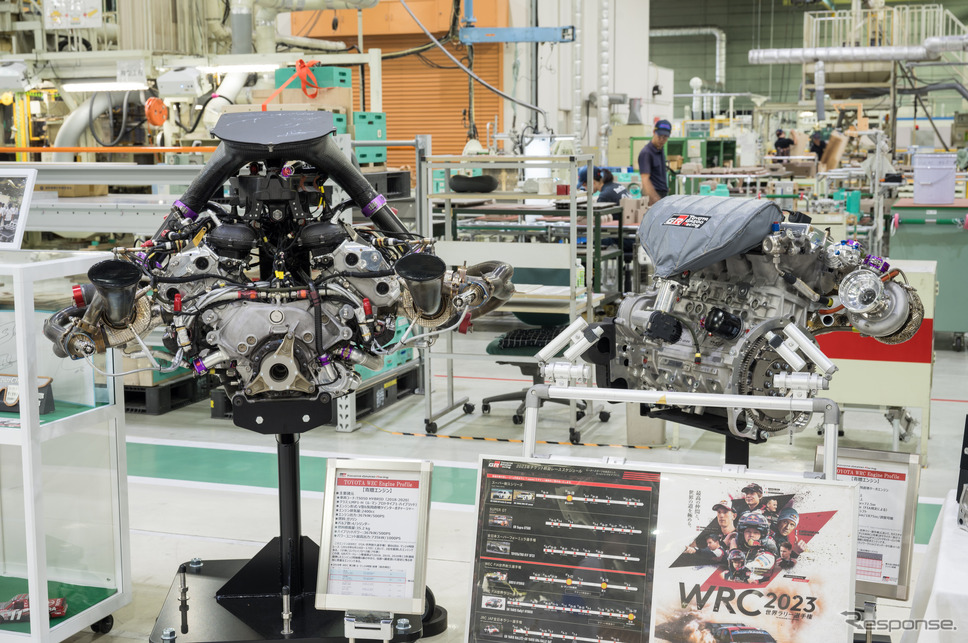
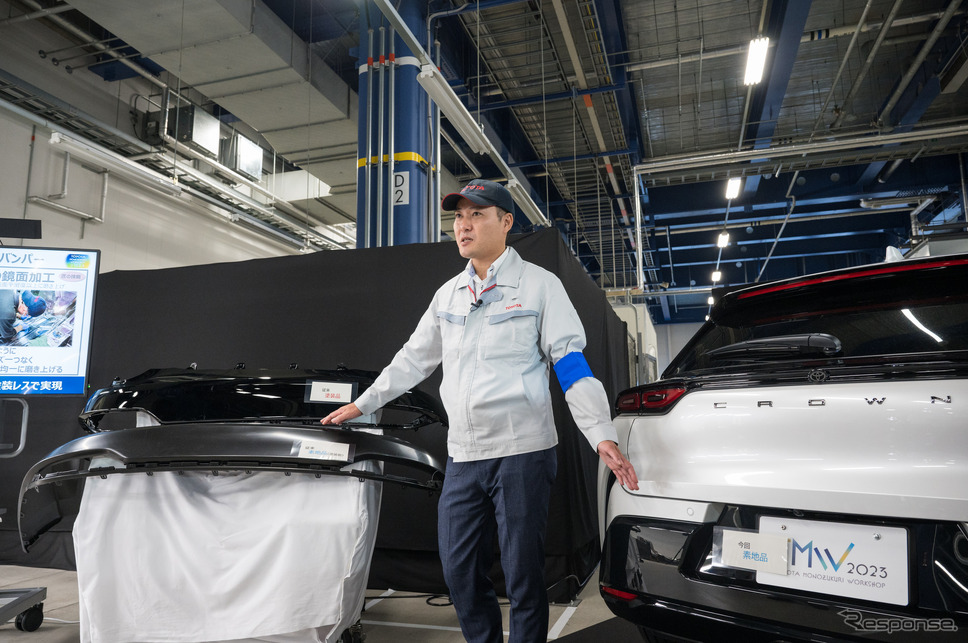
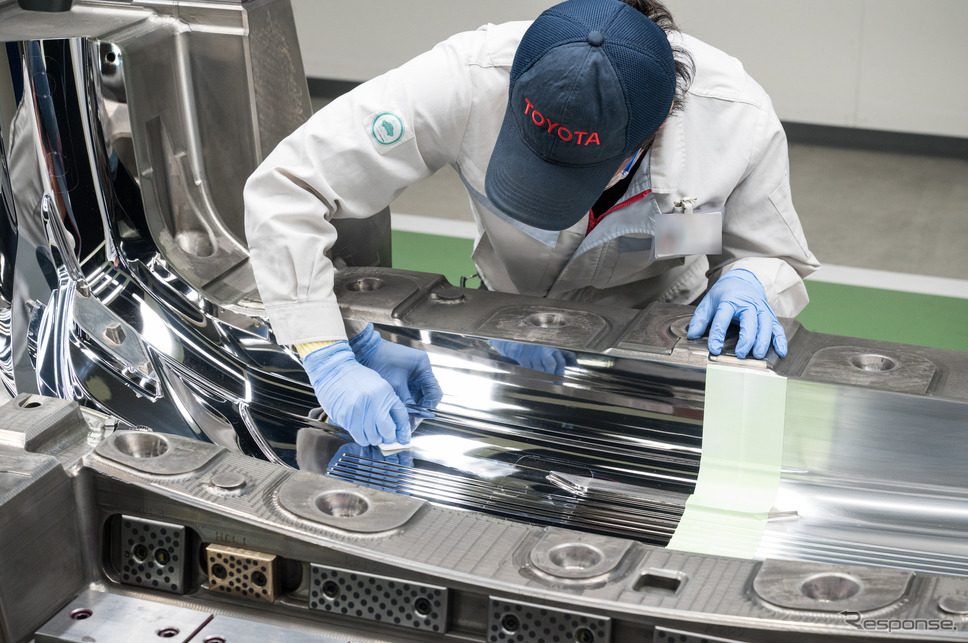
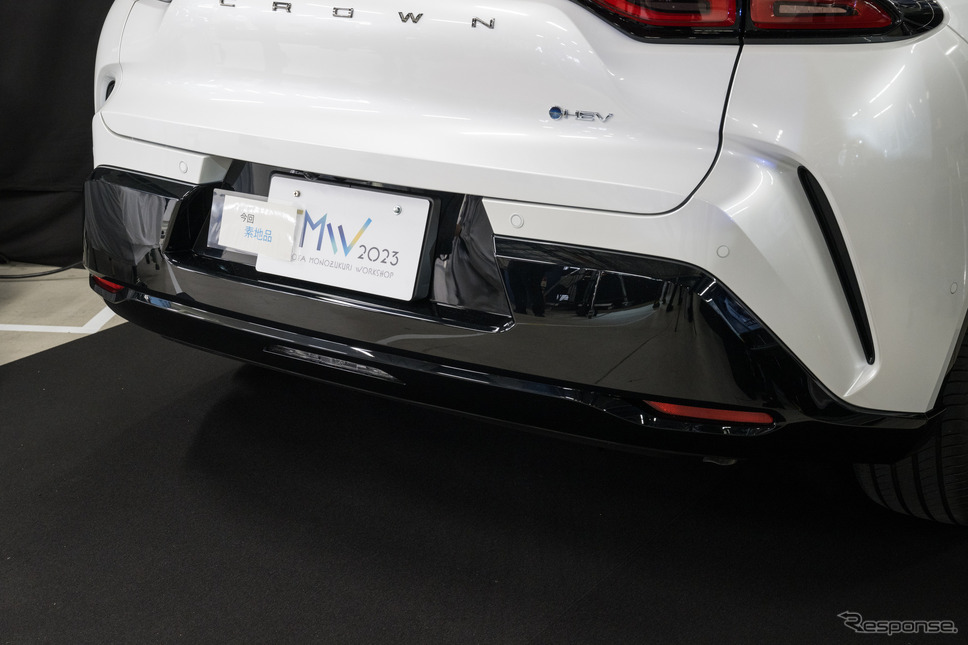
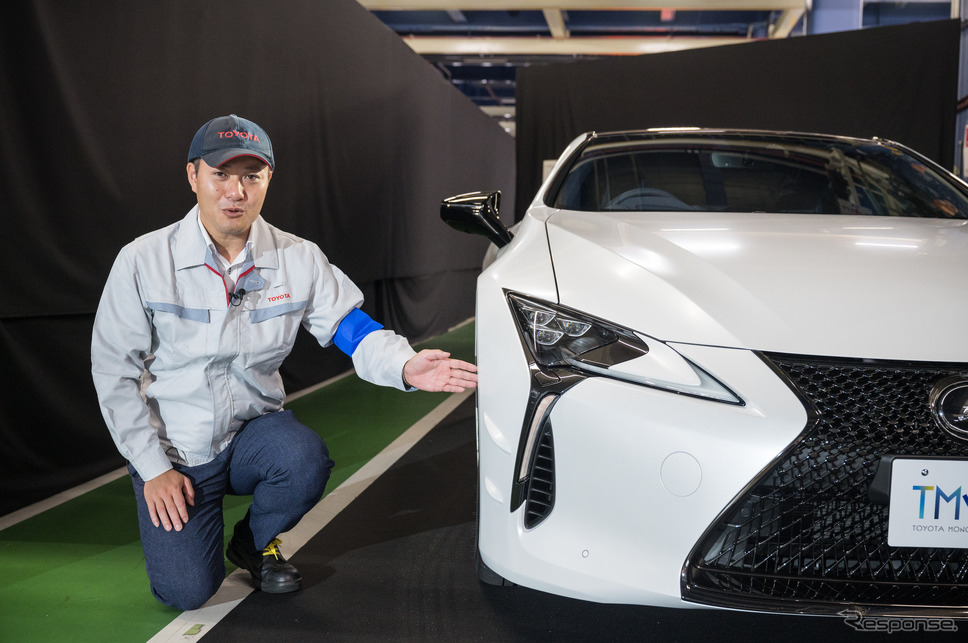
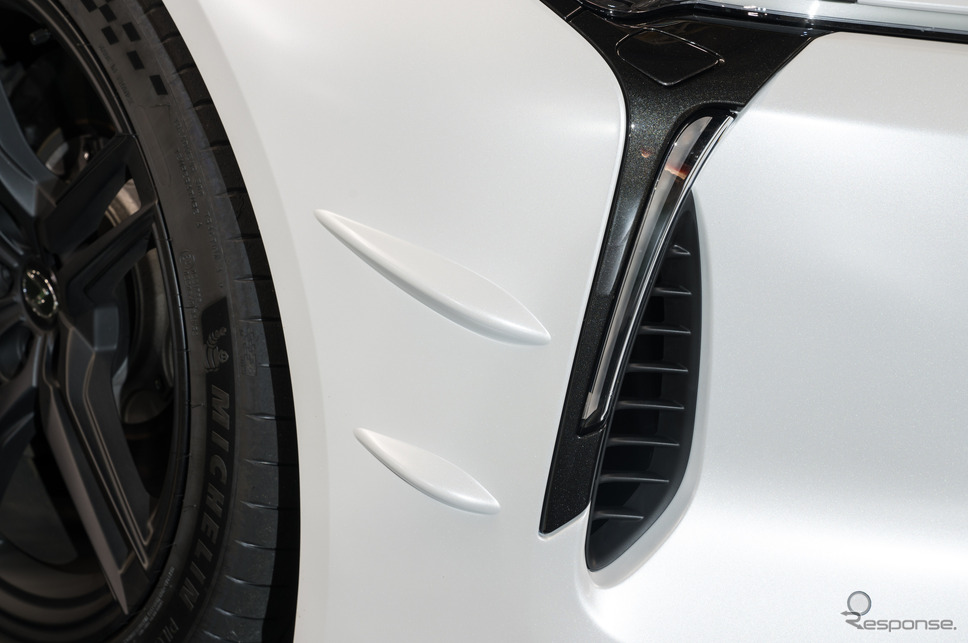
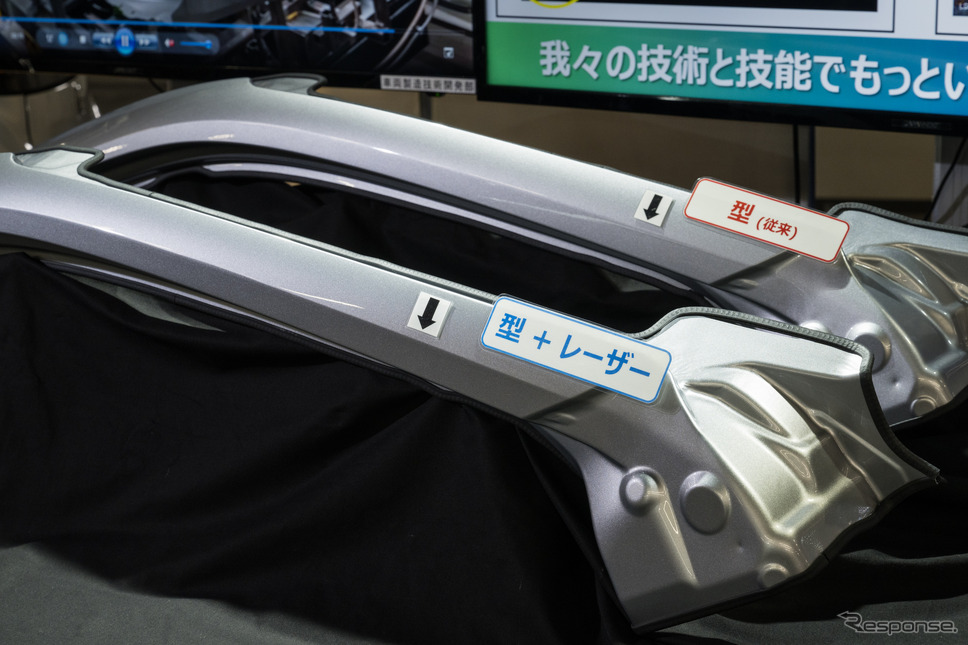
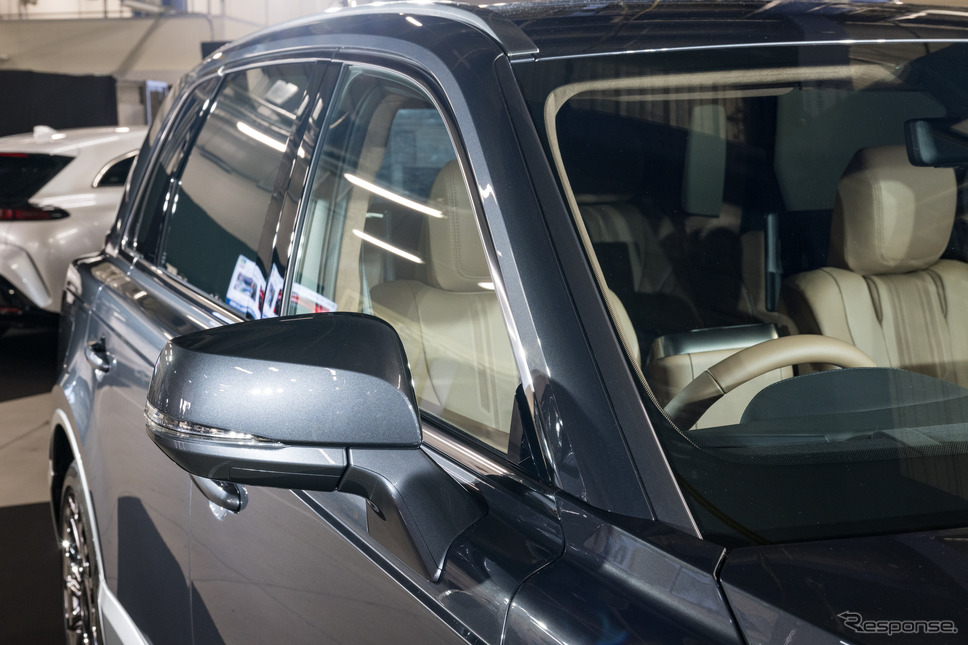
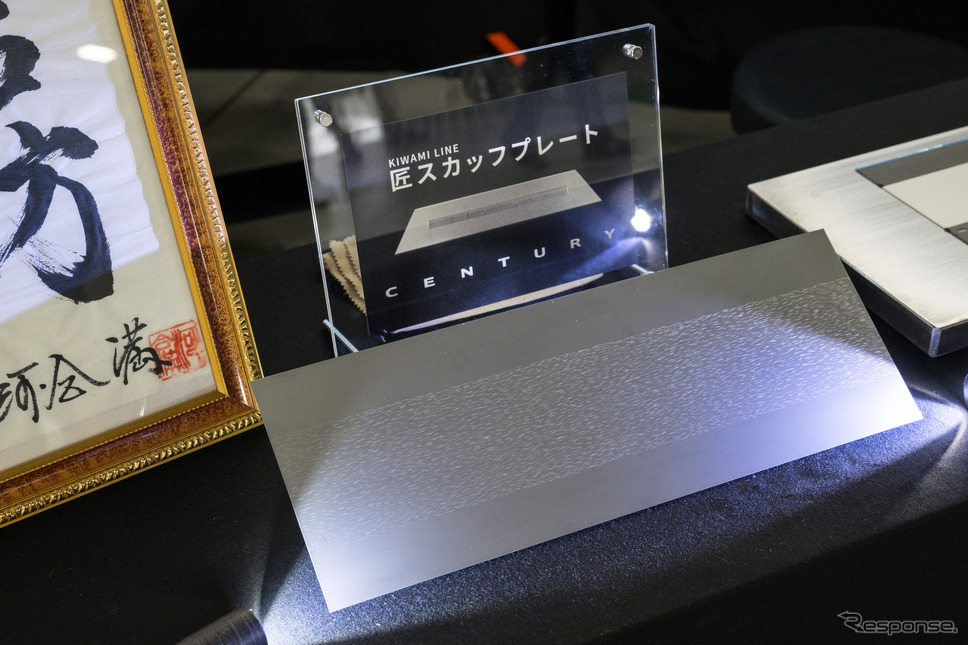
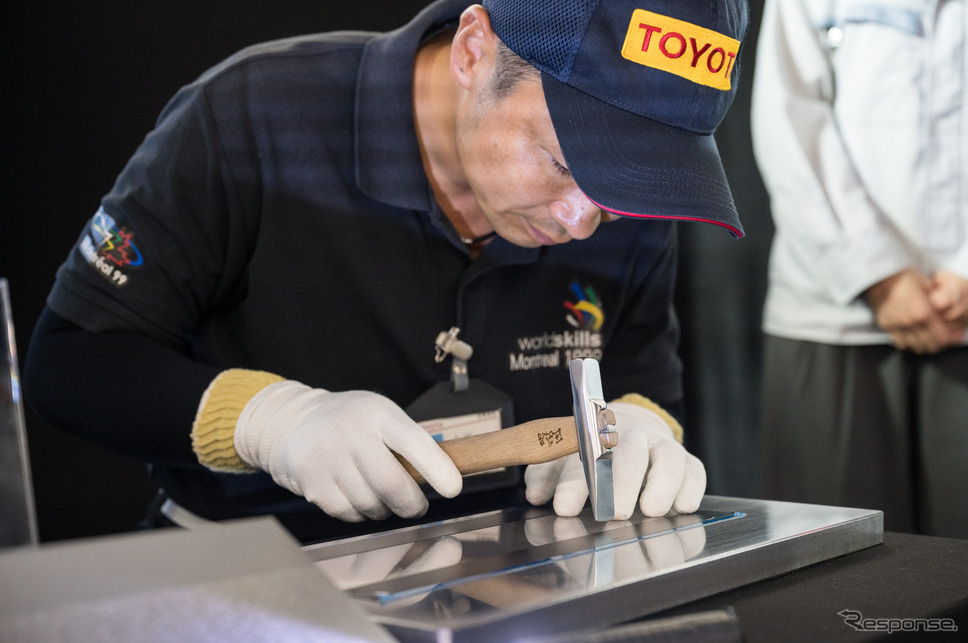
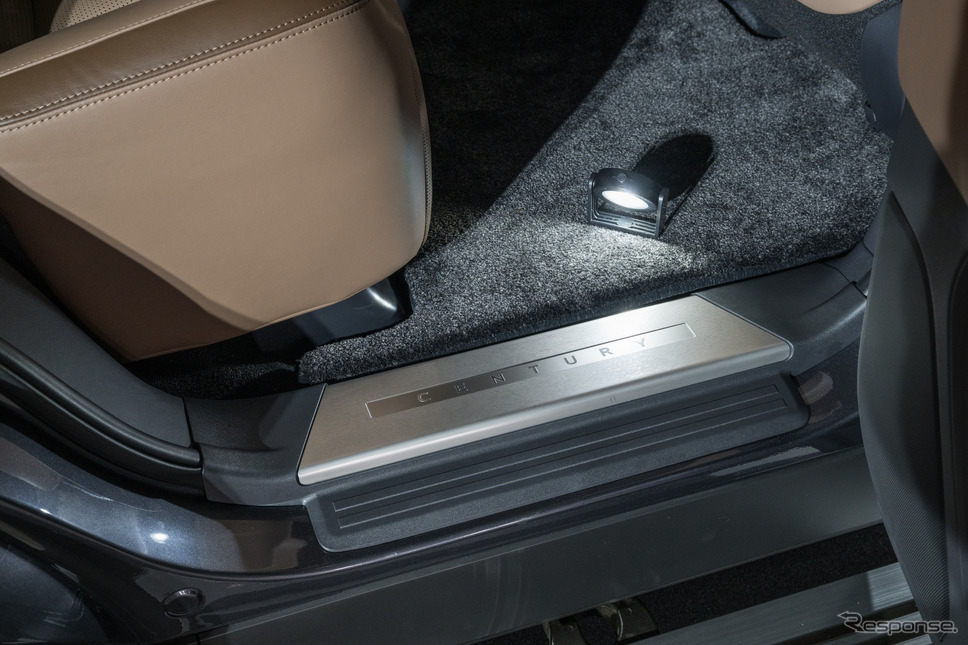
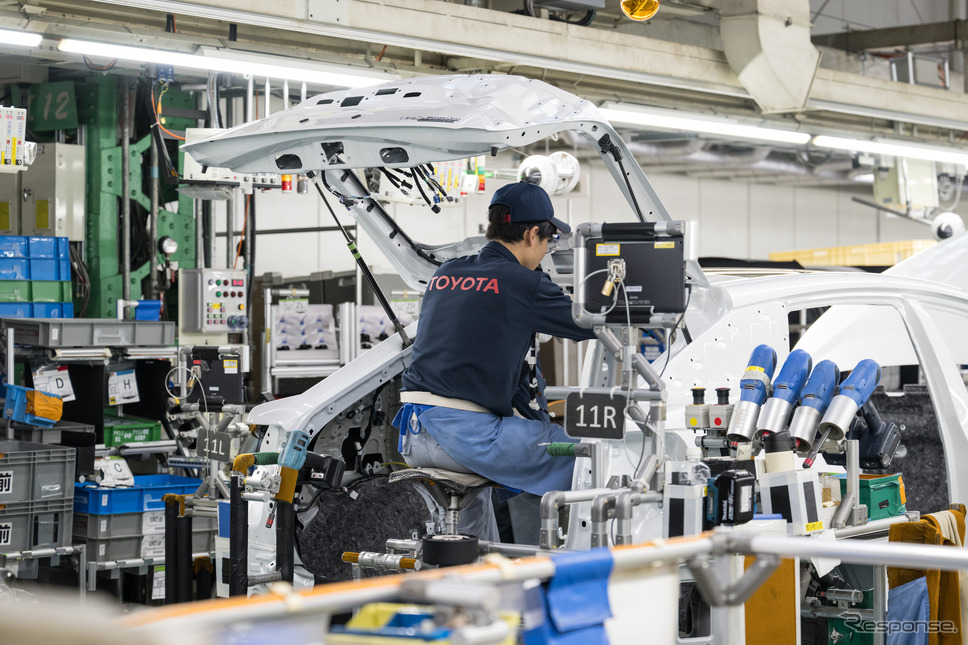
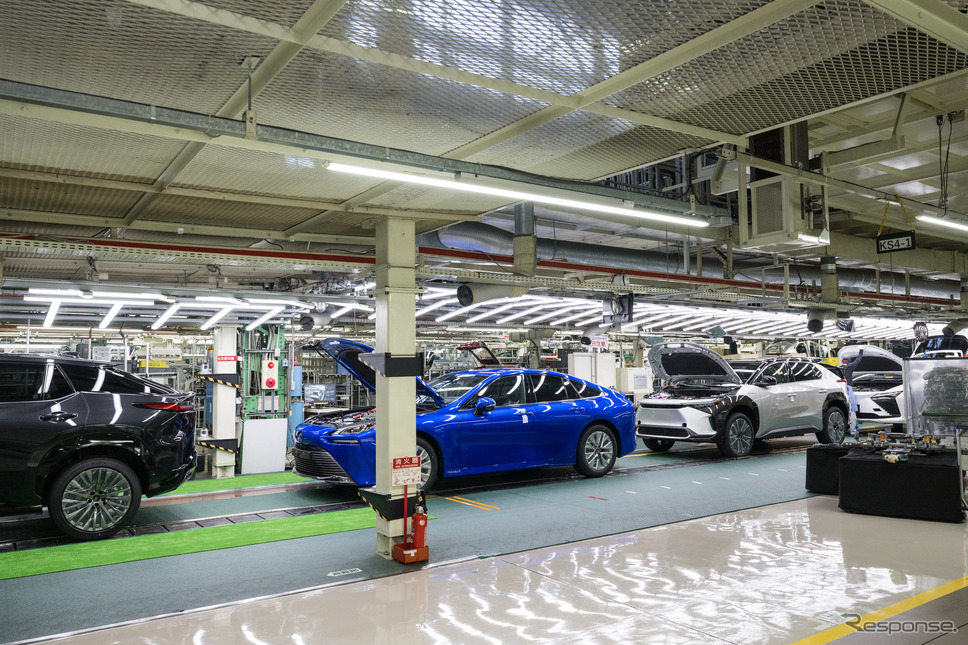
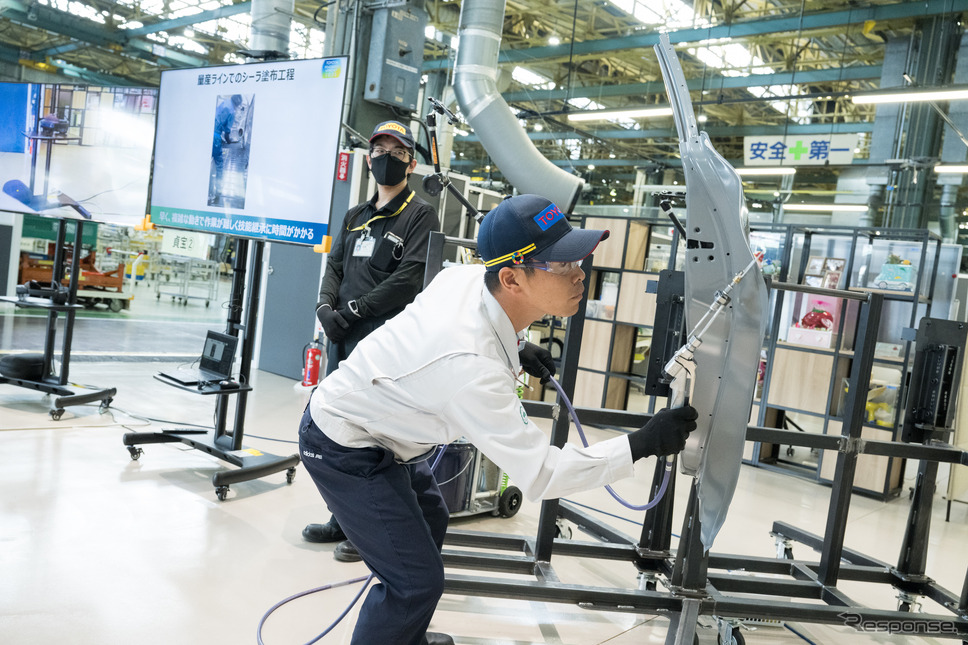
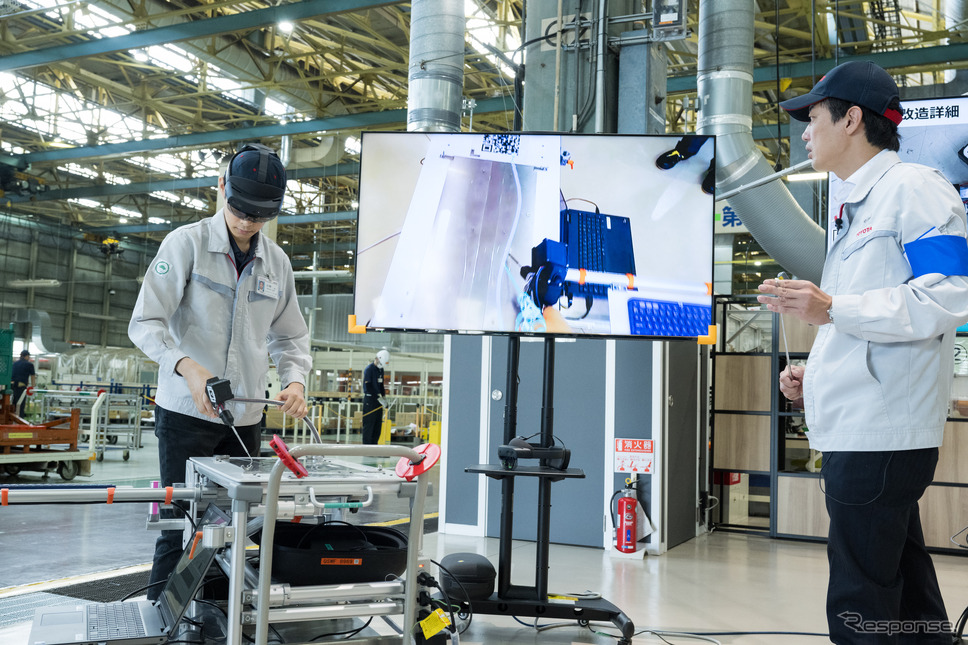
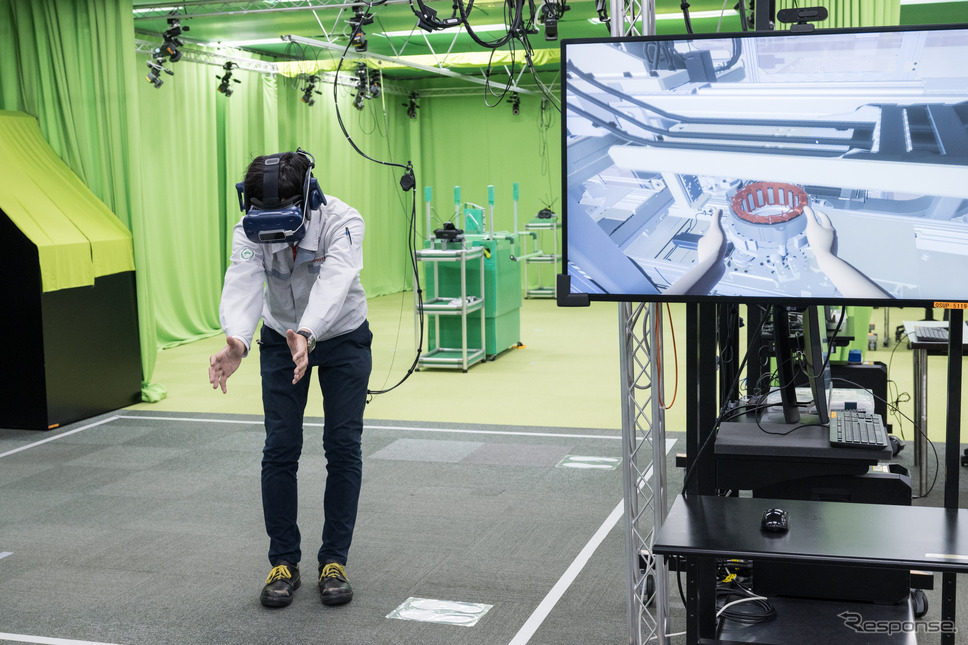
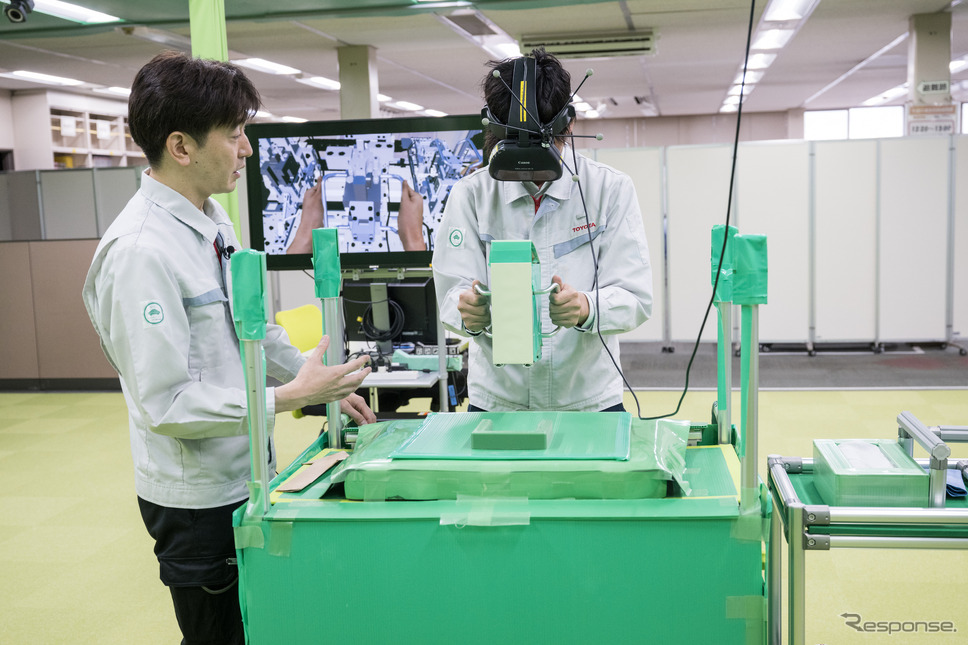
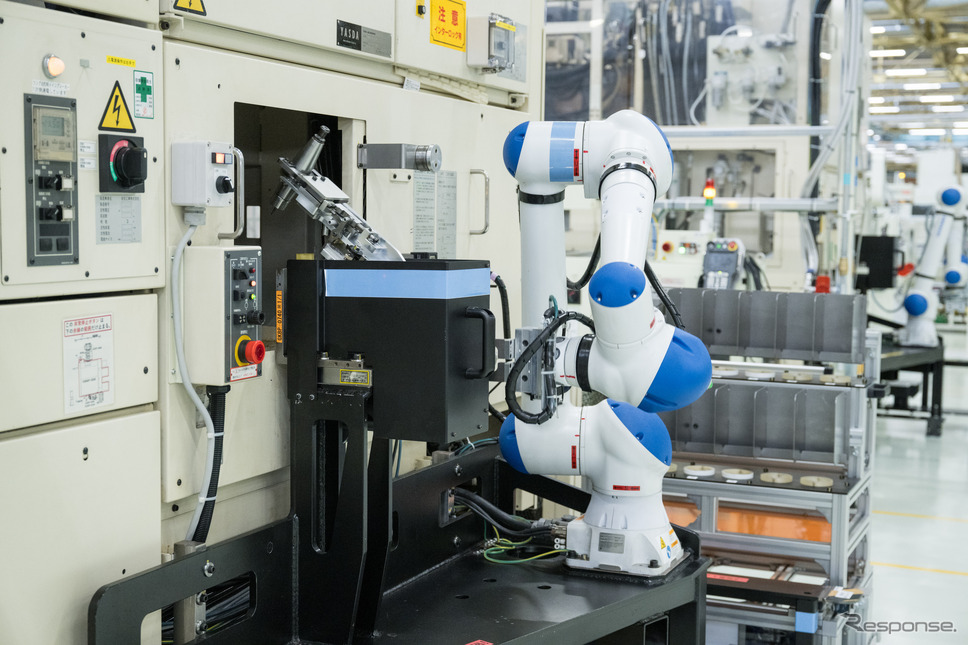
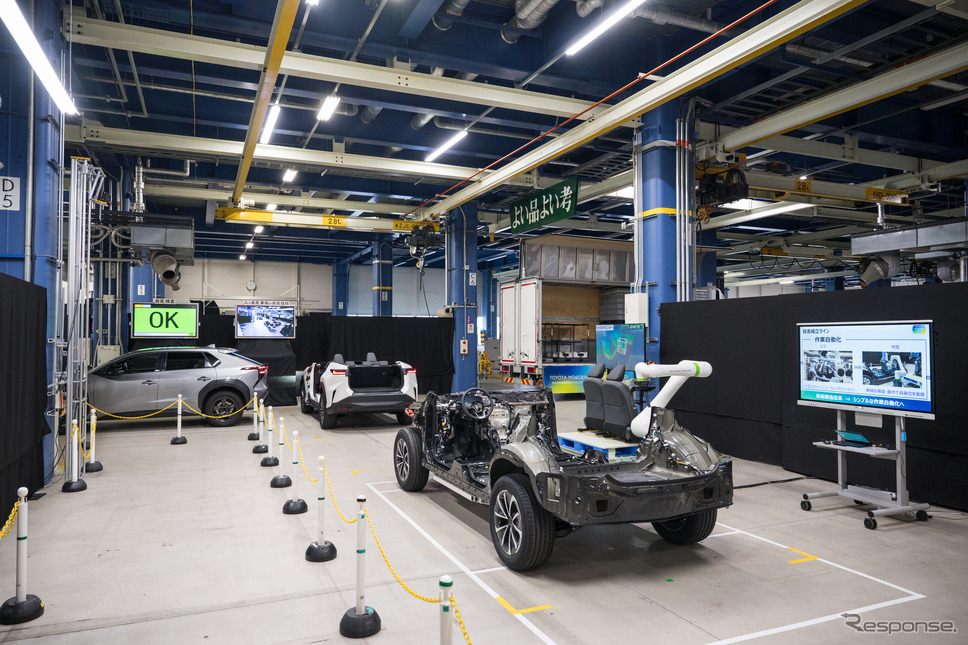
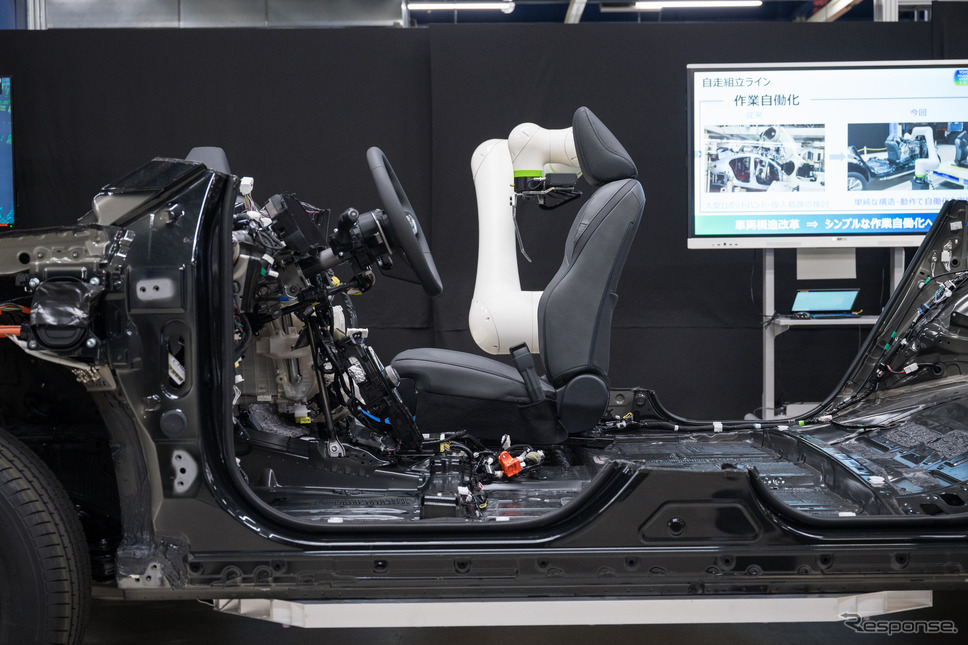
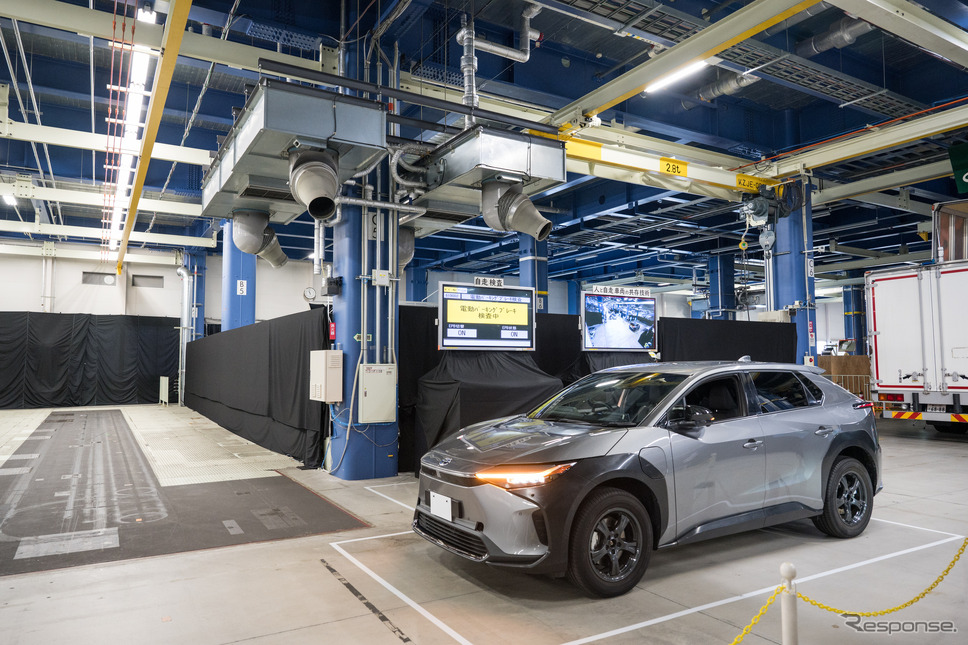

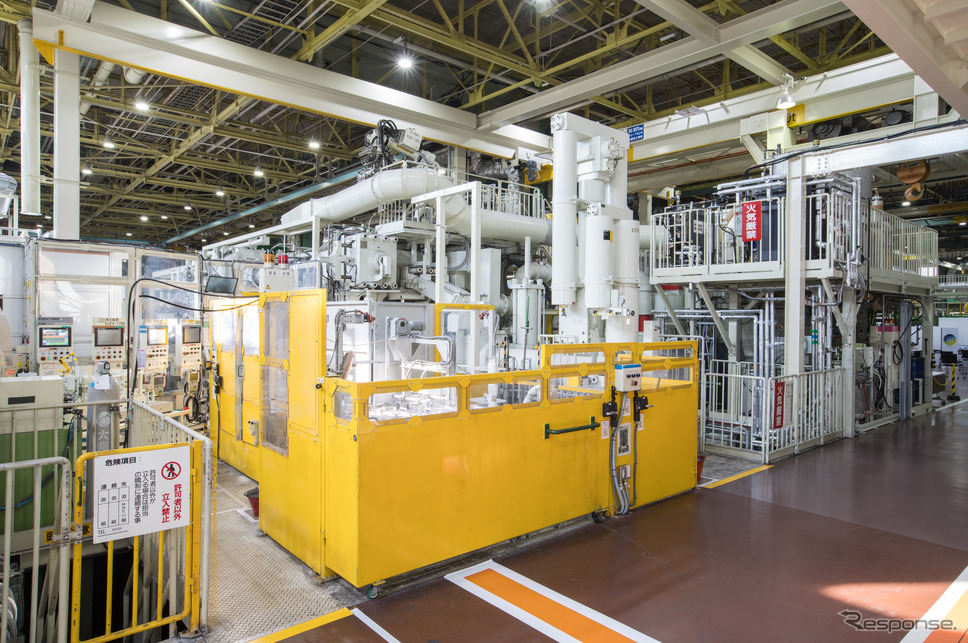
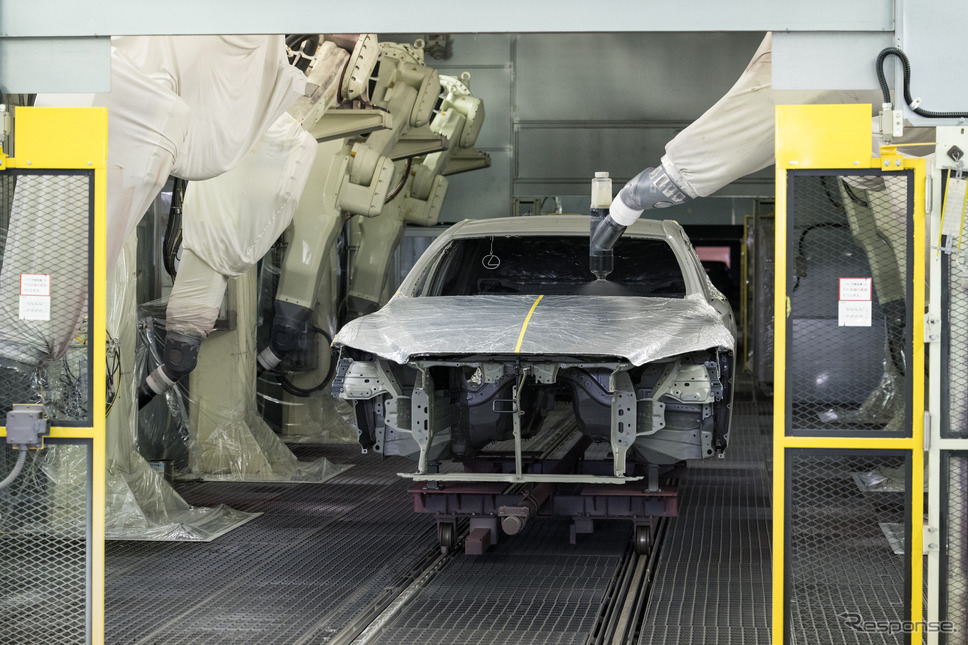
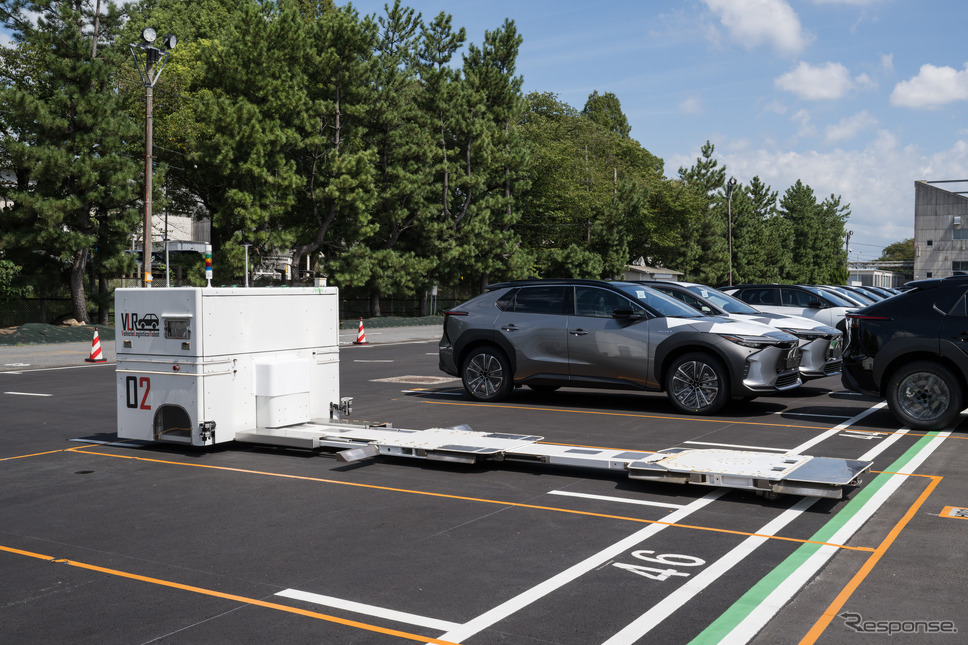
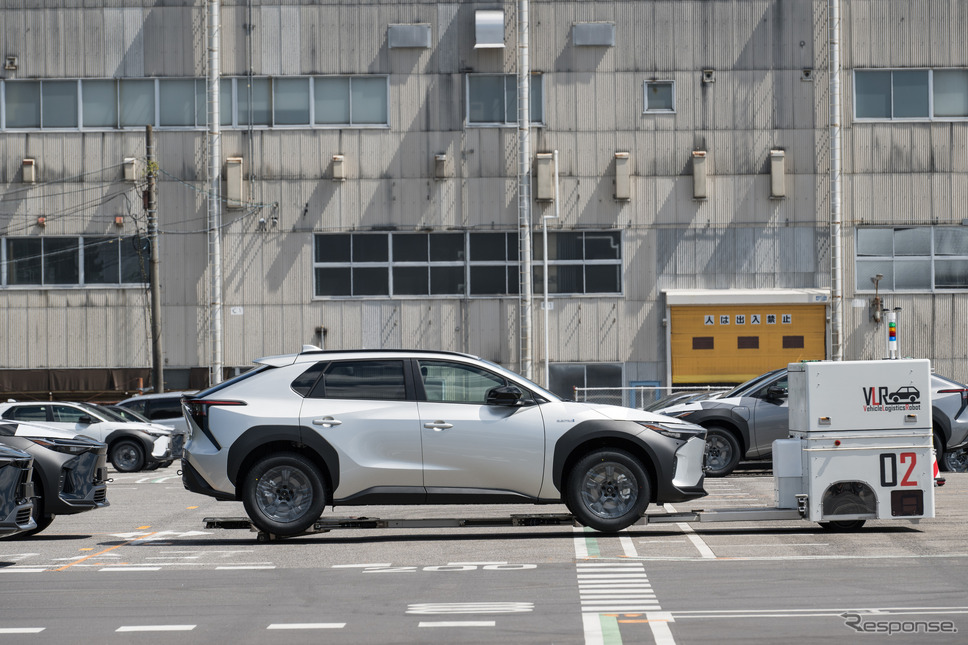
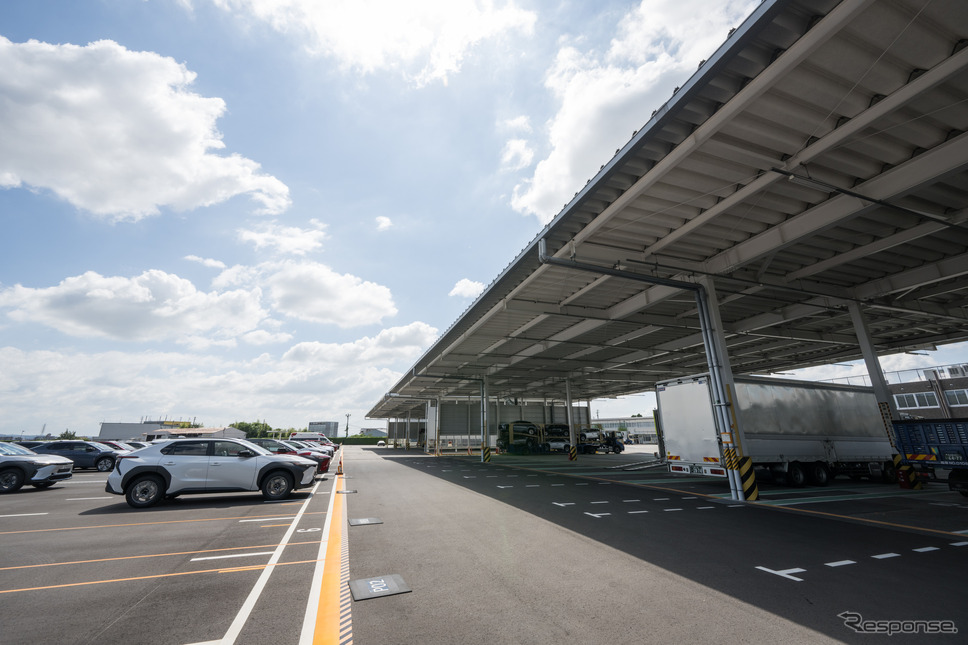
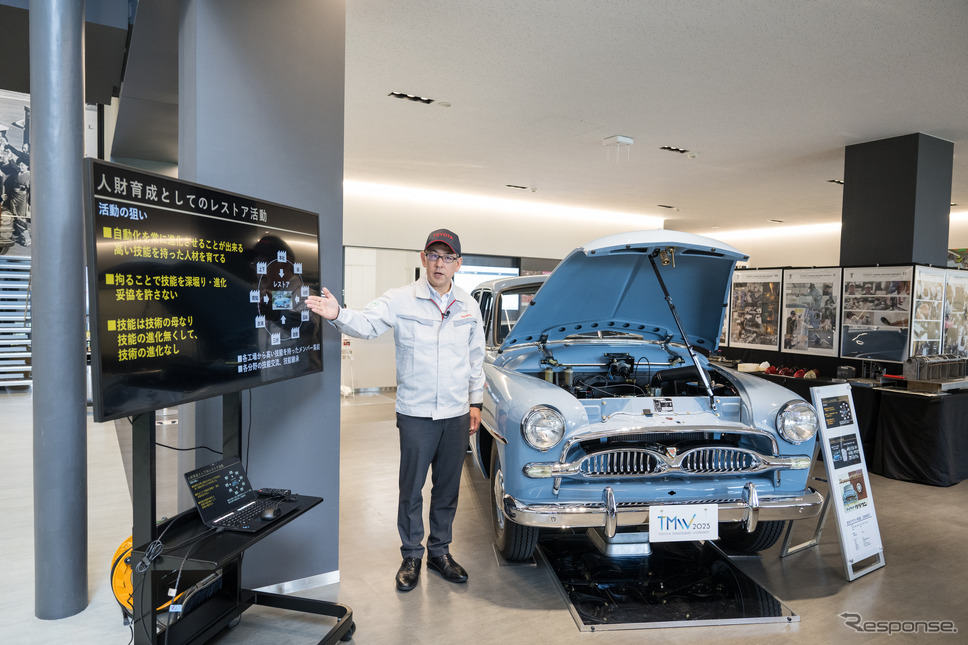
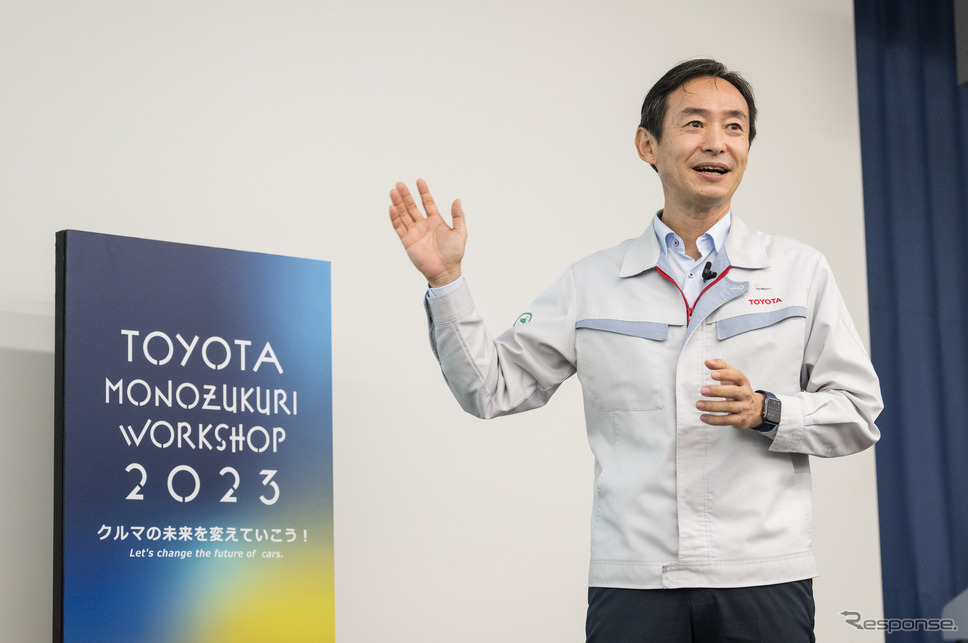
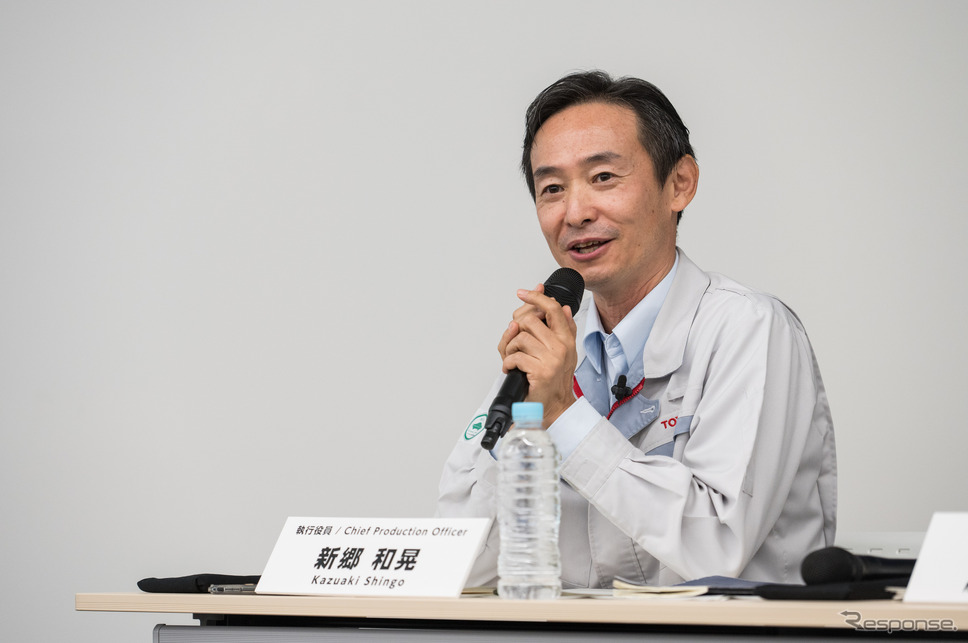